
PLAYFINITY
TECHNOLOGY &
ENGINEERING
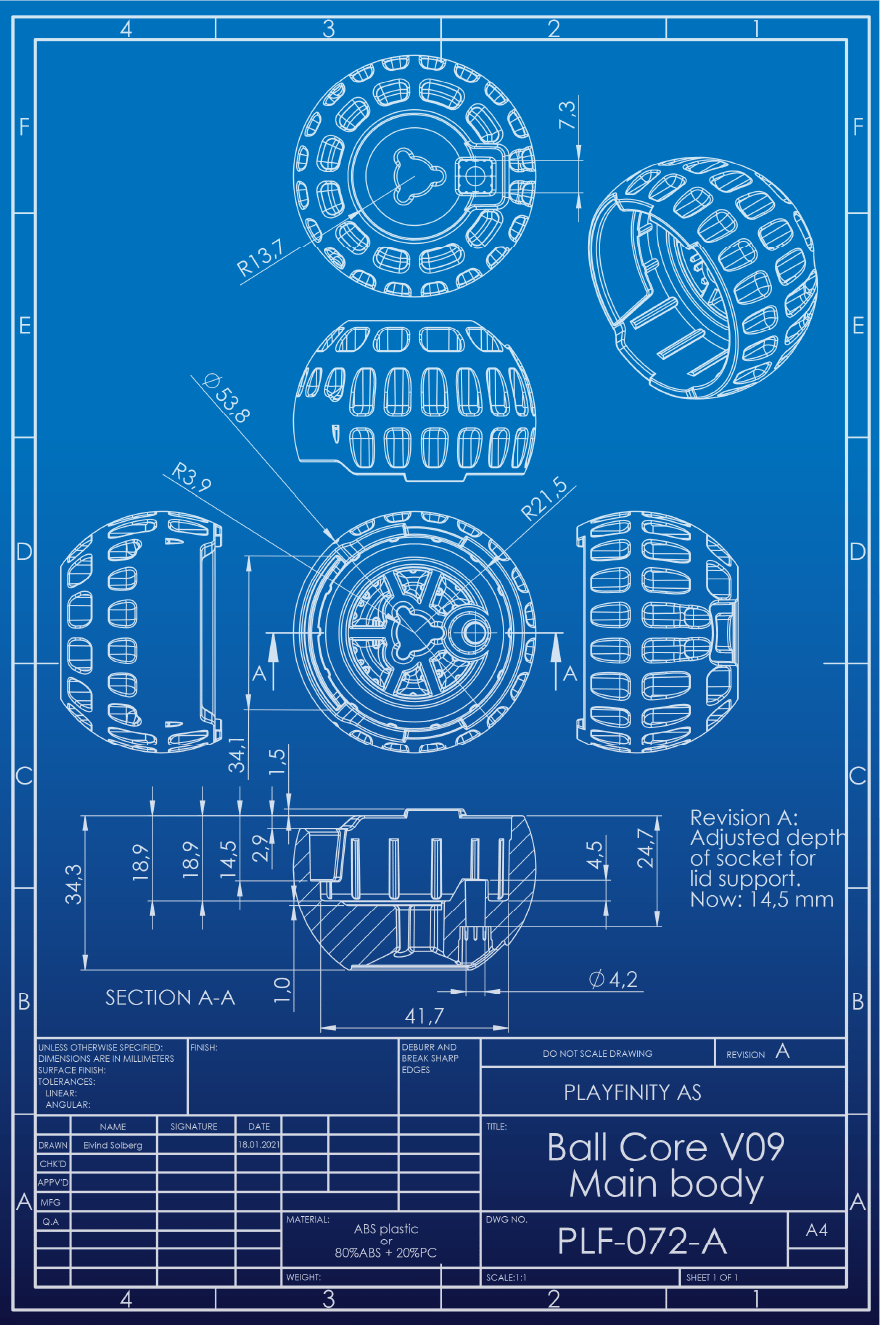
I have a masters in science degree from institute of product design at the NTNU (Norwegian University of Science and Technology). Here I laid a solid foundation for engineering, utilizing my talent for technical subjects, while also enabling my desire for creation, aesthetics and creativity. During my work at Inventas, I worked side by side with a range of talented engineers, bringing my engineering skills to a new level. At Playfinity I had to do all the engineering my self, giving me extensive experience bringing products from idea to market single handed.
Following I will give some snapshots of engineering task i have handle. This will provide some insight to my various engineering abilities.
INTRODUCTION
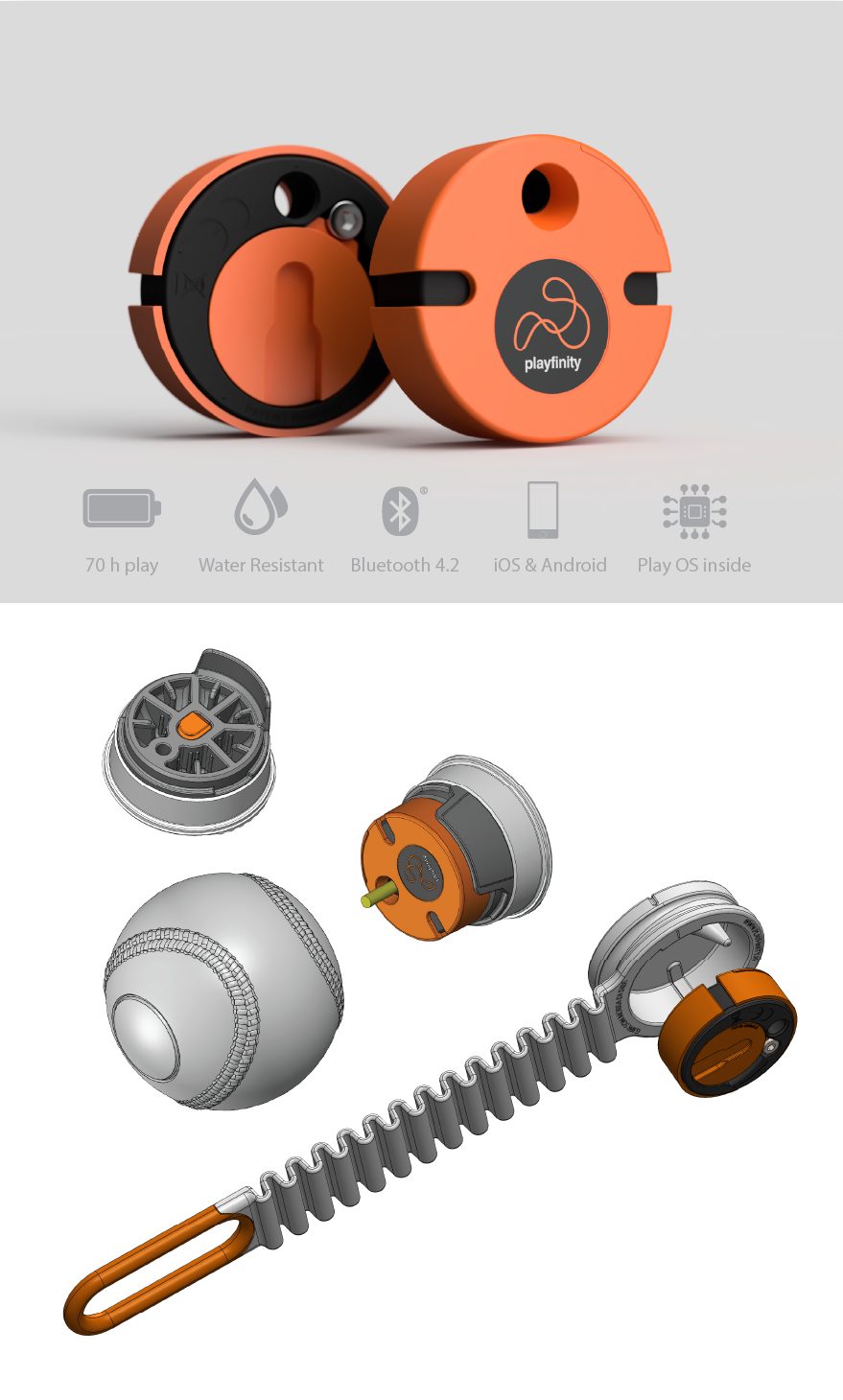
Modeling for injection molding: The construction goal was to make a compact attractive design unit. The parts were to be snapped together for efficient production, and dimensioned for durability. Enabling a integration of electronics with deformation ribs to get precise and ridge hold on electronics. Design a hinged lid with snap function to external units (e.g balls) that would handle hard pull, enable easy snap mechanics, and be compatible with toy certification in regards to child safety.
Double injection mold: To get a integrated button on unit, I modelled for a double injection top part, using ABS plastic for durability and mechanical properties, and TPR plastic on top, to provide nice button function and giving water tight button and water tight seal toward bottom part of casing. Finding right button switch on PCB was important to get right tactical feel compact design.
Inserts and gaskets: I designed for metal insert into bottom part for adding security screw for lid. This was heat welded into plastic. A reeses was added for gaskets under lid and between casing parts to obtain water proof casing. Tests shots of parts provided for adjusting recess to give correct amount of pressures on gaskets.
Supports and mechanics: A lot of work and testing went into supporting the battery and contact points so that the unit would function under extreme impacts. Defining battery connector and adding through hole support through PCB were essential design details.
VDI and Tampong print: VDI values were provided to get right surface aesthetics. Tampong printing used for two colors on top part of casing.
Patent: Sensor casing design was was patented in regards to its multi function qualities and system design for activ gaming gear.
Skill sets: Modelling for injection mold, Construction for durability and water resistance, Construction for snap assembly, Rapid prototyping and 3D printing, Aligning production foundation for production facility. Production follow up.
INJECTION MOLDING
THE SMART
ACTIVITY TRACKER
Water resistance - Construction for gaskets and TPR geometri to obtain water resistance
Lid strength - dimensioning threads and hook detail to give fastening mechanism to external equipment. Underwent several iterations of testing and redesigning to match specification.
Button function - Iterations of testing button components and flex in ABS plastic to get right button tactility and robustness.
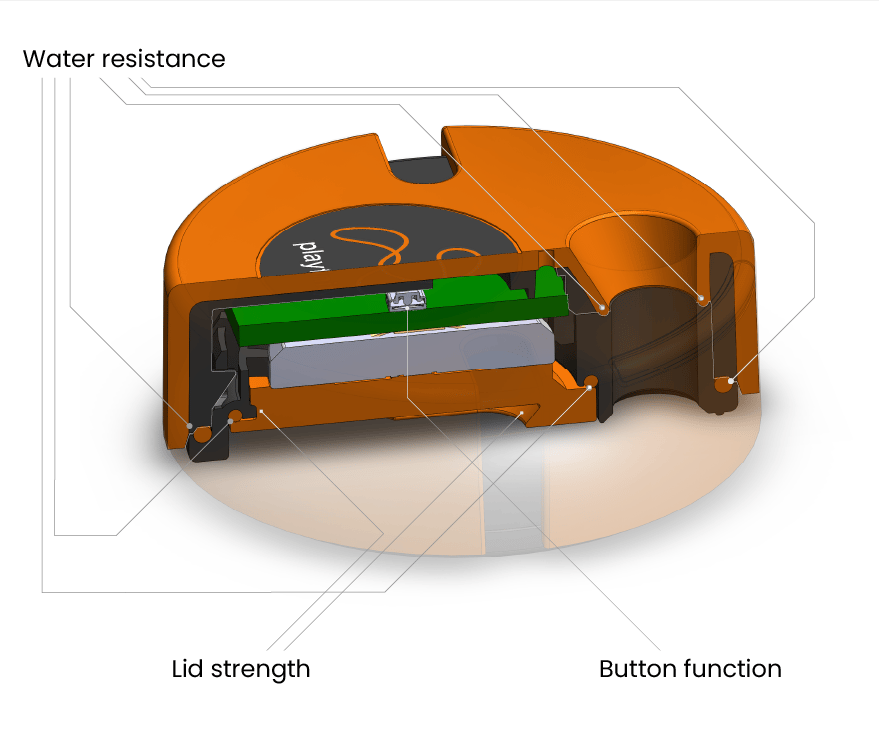
Snap assembly - 4 x snap connections for strong connection
Heat welding - Well dimensioned for heat welded metal insert for screw hinges
Water resistant - Construction for pressure on gasket to obtain water resistance
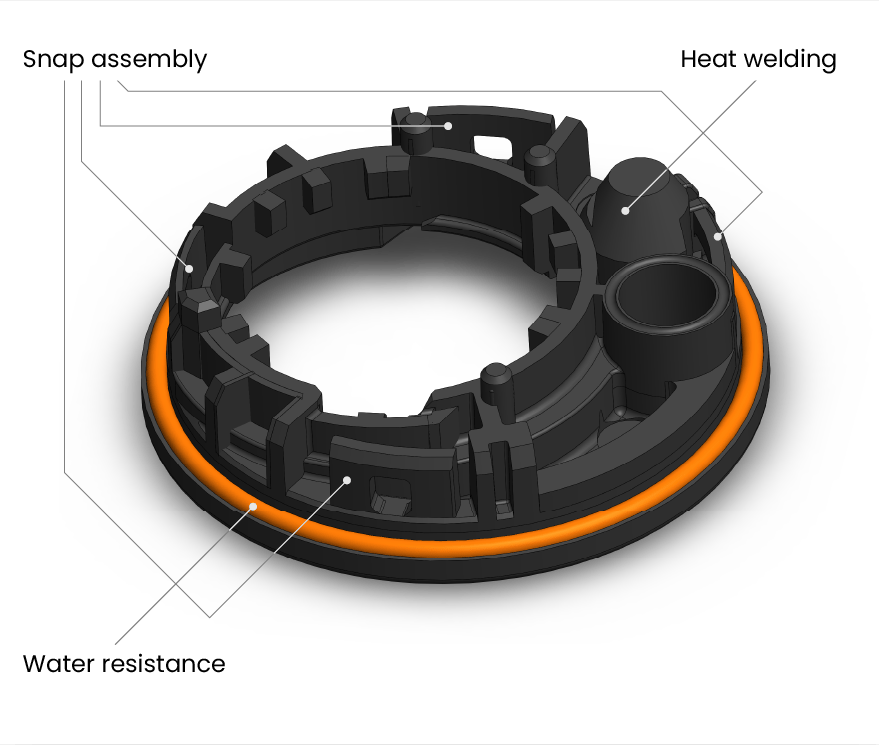
Battery supports - Reinforces battery support for secure electrical connection under extreme impacts
Robust connector - Iterations of testing connector components and corresponding casing design to get robust connectivity to button under extreme impacts.
Metal insert - Heat welded metal insert for screw threads
Water resistance - Construction for lid threads to give sufficient pressure on gasket to obtain water resistance
Sliders - Added 0,3 mm knobs on the surface of bottom part of casing to enhance gliding feature when the smart is used as a sliding puck game.
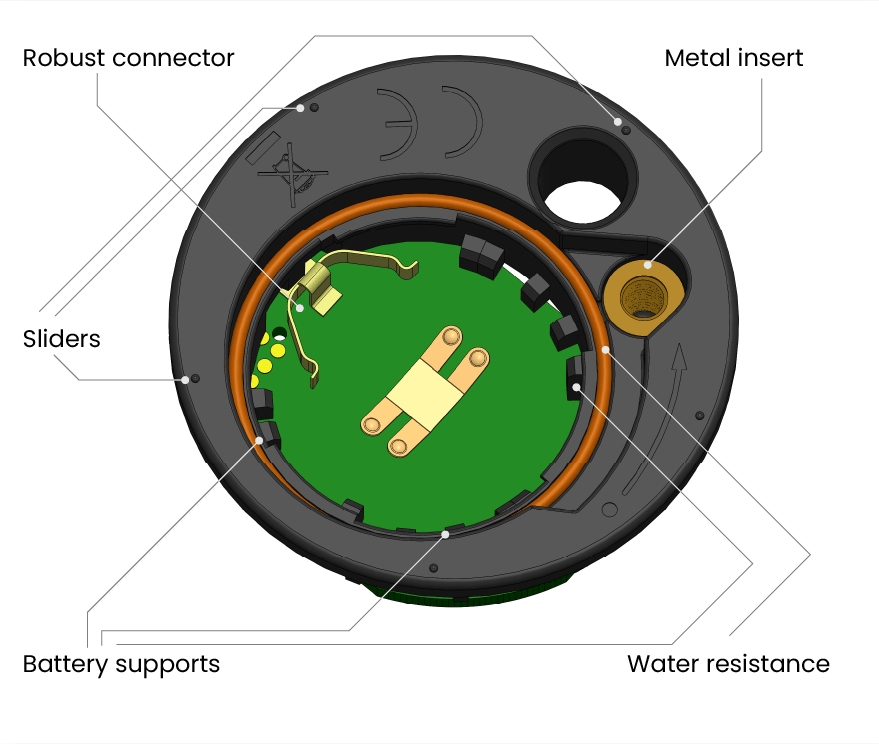
Robust power connection - Through hole support on PCB to minimise movement. Iterations of designing casing to maintain secure connectivity
Compact design - Iterations of configuring layout of components on PCB, PCB design and designing mechanical functions to get compact design with right level of robustness.
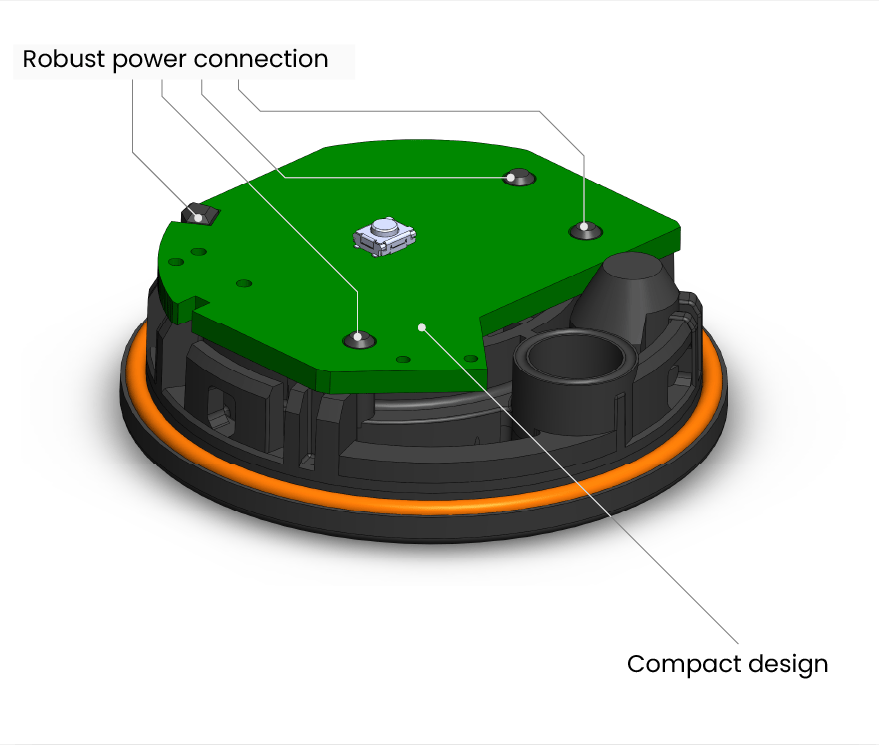
Side button - Enabling a side button function by taking advantage of the dobbel molded properties. Abs plastic keeping shape and button press tactility, and TPR to allow movement.
Light emission - Use thin areas in TPR to let light pass through, minimizing parts and maintaining water resistance
PCB fit in casing - Deformation ribs to allow tolerance for tight hold on PCB, minimizing movement under extreme impacts.
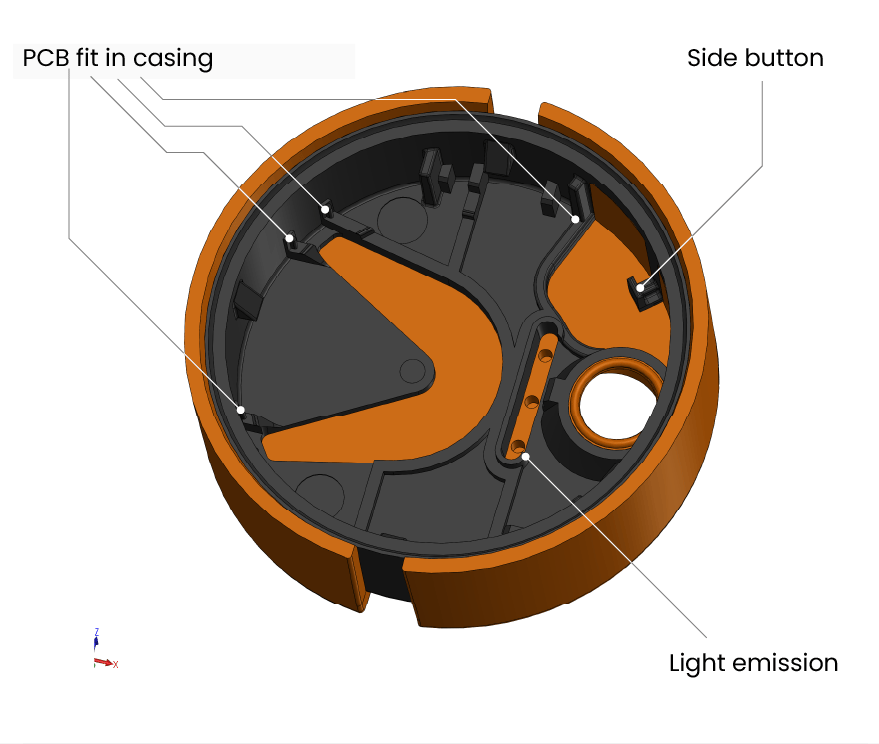
The smart is a core unit for our Active Gaming system. Adding this to various playware objects is important for the expansion possibilities for the gaming system. Hence, I had to make room for various fastening mechanisms. In addition to the slide and twist snap functions visualized above (which were prototyped and tested to withstand 20 Kg pull ), I had designed for clips function to side slots on unit, as well as a screw hole enabling a screw to fasten unit, or to screw a lid over unit like done with the baseball.
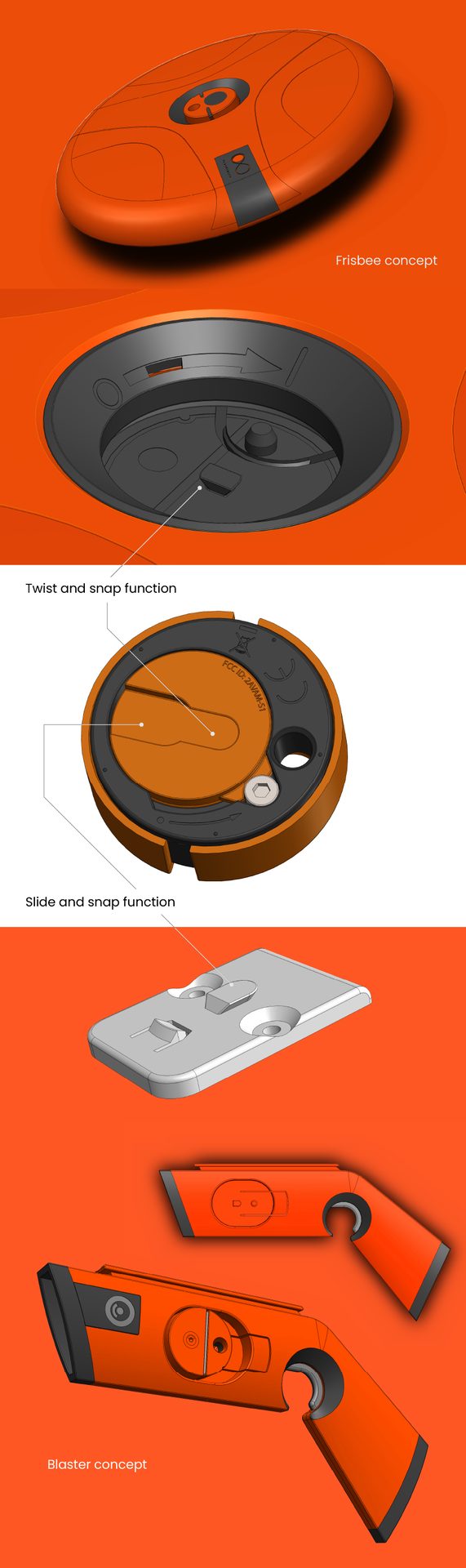
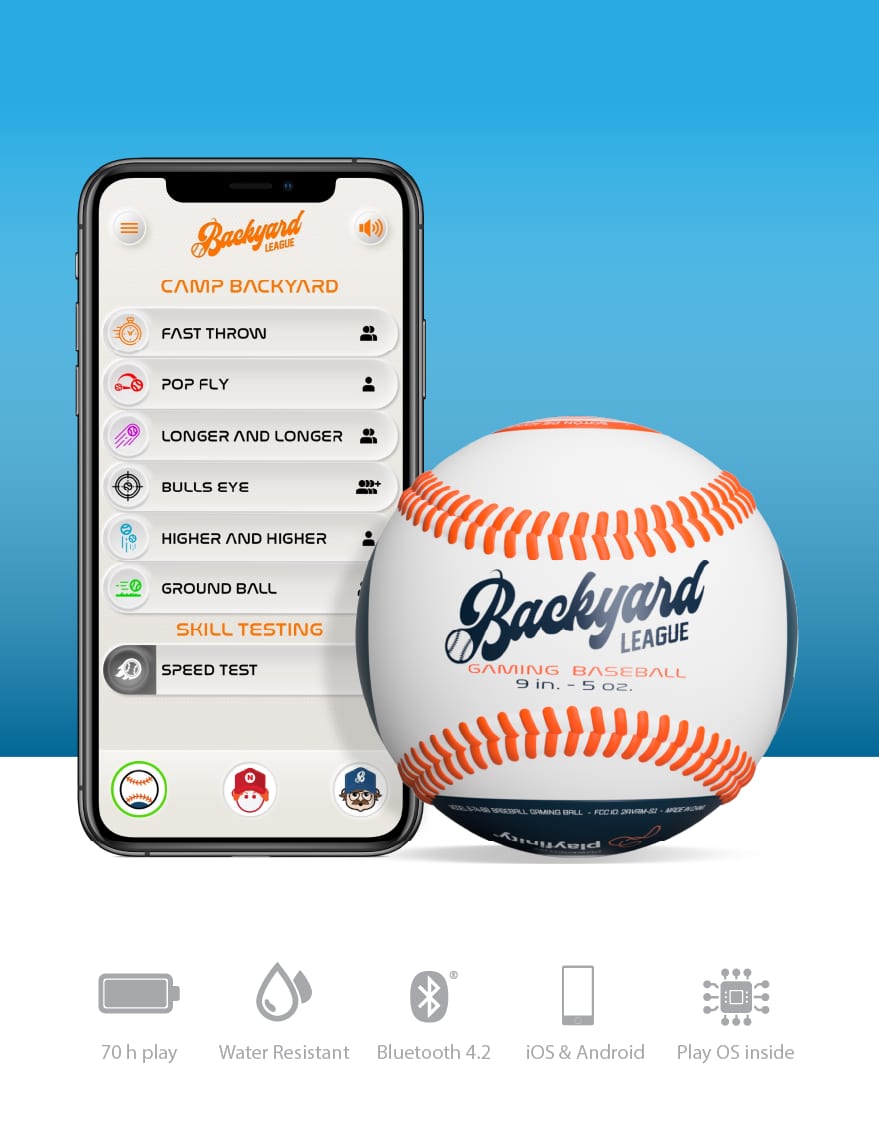
Modeling for injection molding: The core and lid were optimised for injection mold, and minimising parts. TPR parts were added to give functionality (button function and robust snap function for fastening activity tracker) as well as keeping core senter free from PU foam when over molded. Experimenting with shore values on TPR was essential to get the right function on button and mechanical properties for fastening the activity tracker to lid.
Weight adjustment: We wanted the ball to be regulation size and weight. PU foam has a varying end result as to weight. To face this, I added pockets for entering 16 set screws, allowing to evenly add 16 grams to ball for obtaining optimal weight. Experimenting with PU mixtures was also a key part of this process for right weight, shore and surface quality.
Universal tool: I had costume made a tool for the packaging, providing tool for phillips screw on lid and set screws on activity tracker and weights. Investigating right metal qualities and production methods versus stand available components was a key task.
Patent: Baseball design was patented
Skill sets: Modelling for injection mold and multiple part overmold construction, Investigating plastics for right characteristics, Rapid prototyping and 3D printing, sourcing production facilities, communication with chinese manufacturers.
DESIGN FOR
OVER MOLDING
GAMING BASEBALL
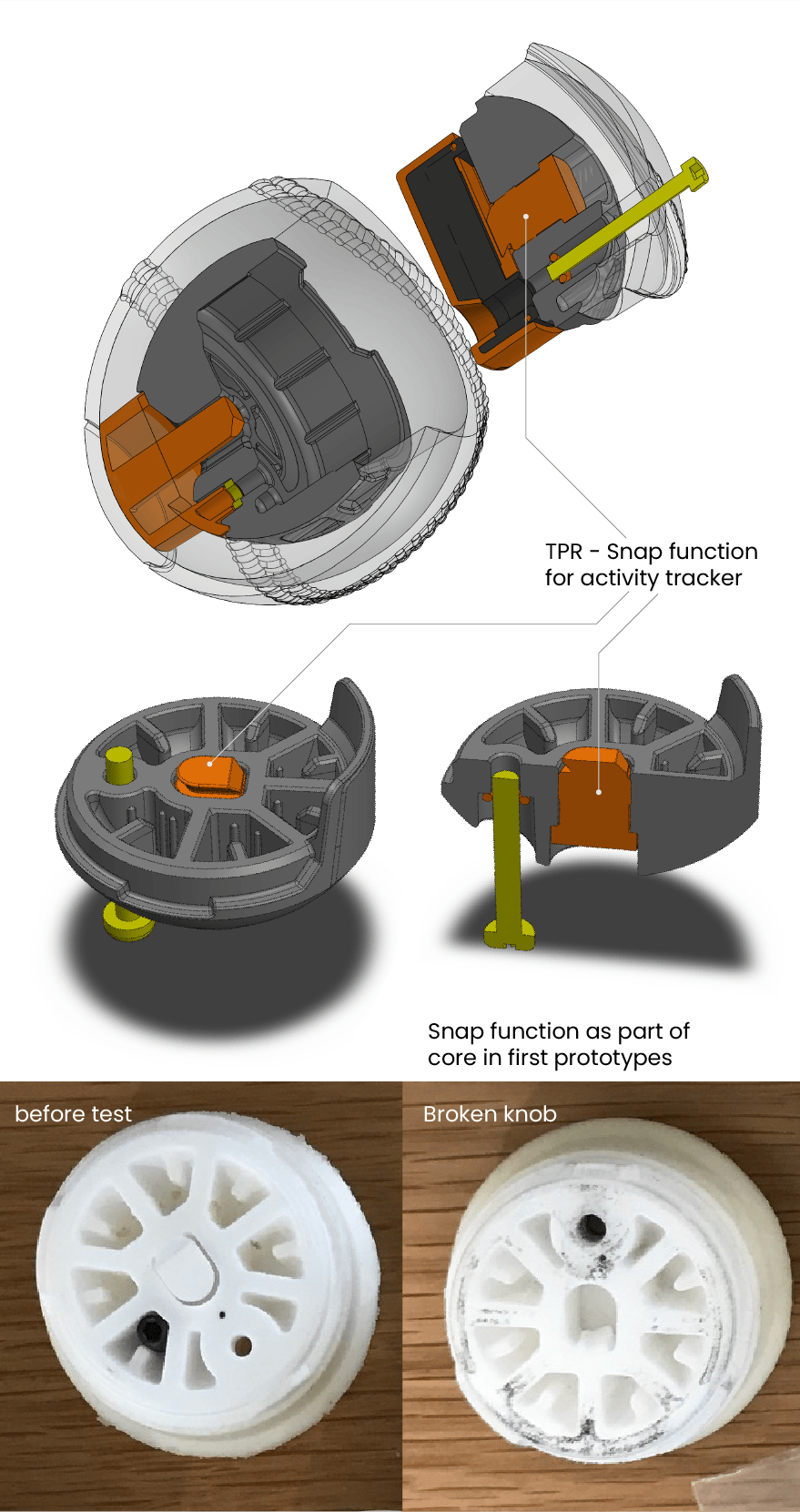
Testing prototypes of baseball revealed that the fastening knob for activity tracker was a week point. Hence redesigning core with both button and fastener as TPR parts became a crucial engineering decision to achieve a robust end product.
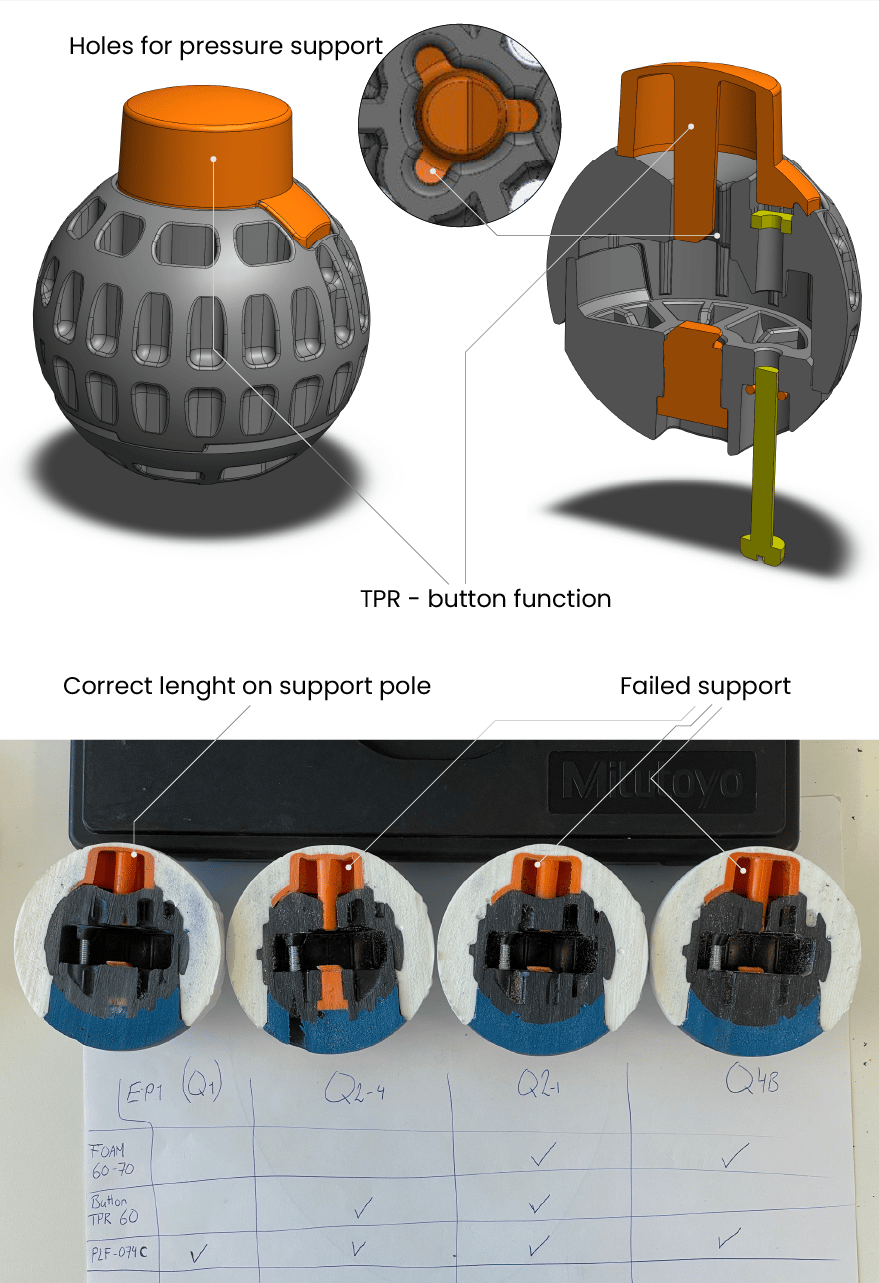
Creating a button function on a hard baseball was challenging. After concluding on method, exploring TPR geometry and shore, together with height of TPR part was crucial. I had anticipated that pressure from foam expansion under molding would be an issue, pressing the soft TPR part down. Hence I made room for three support rods to be added to molding tool that would pass through ABS core and be able to support the thin TPR “roof” of the button. The challenge being to find the right height of rods.
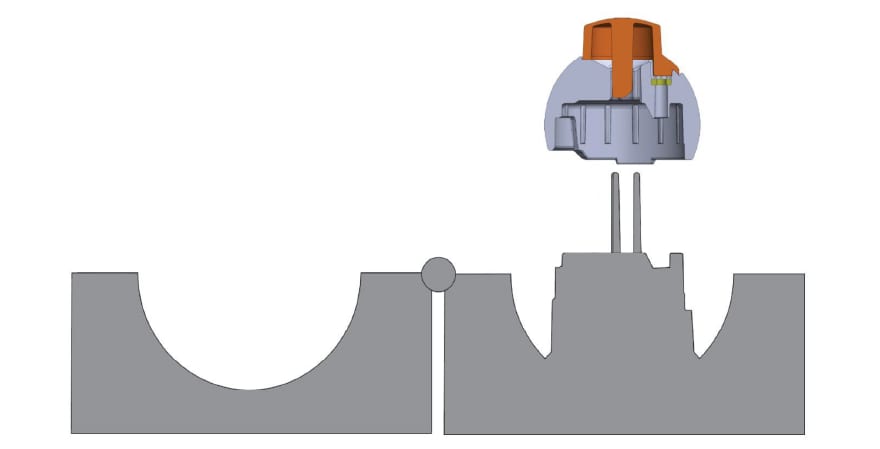
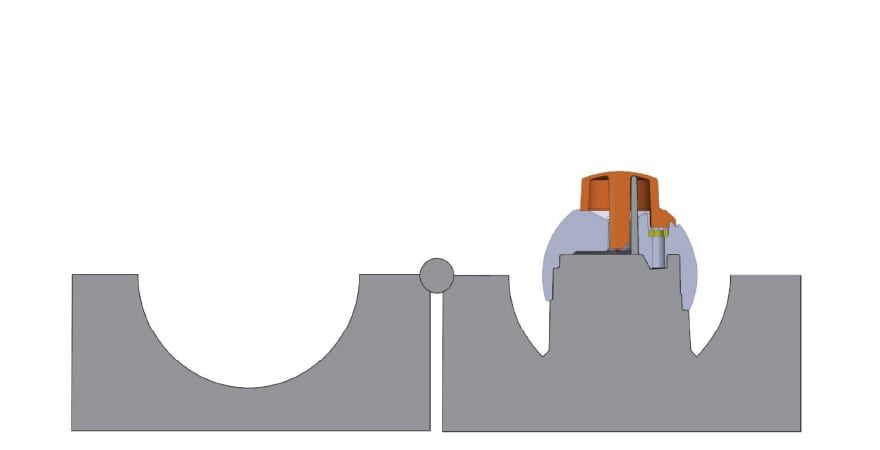
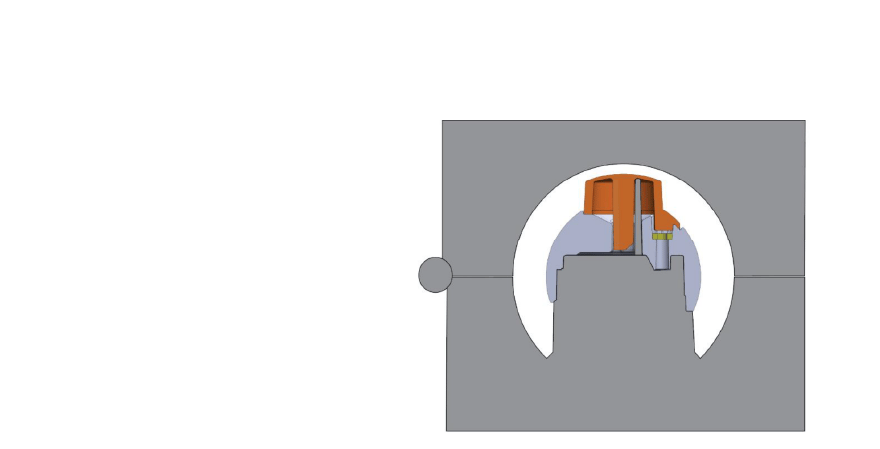
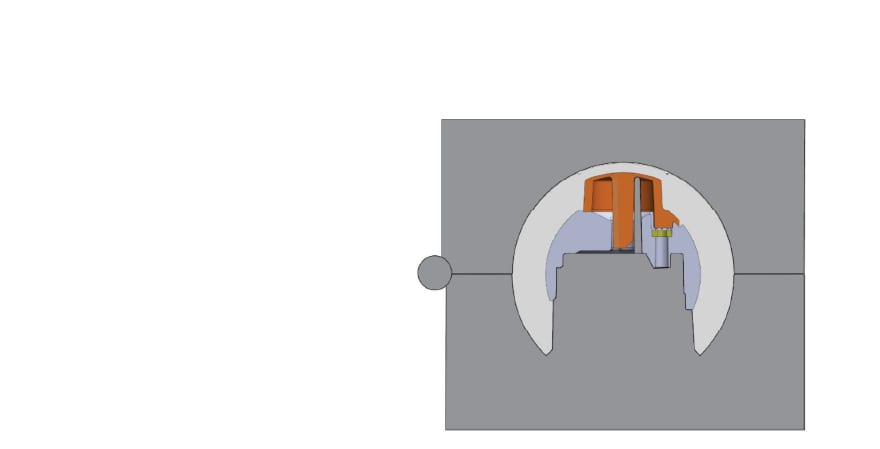
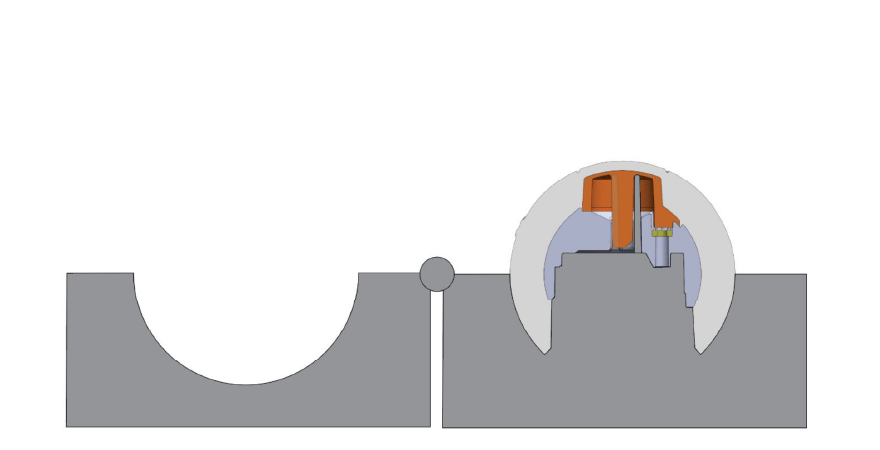
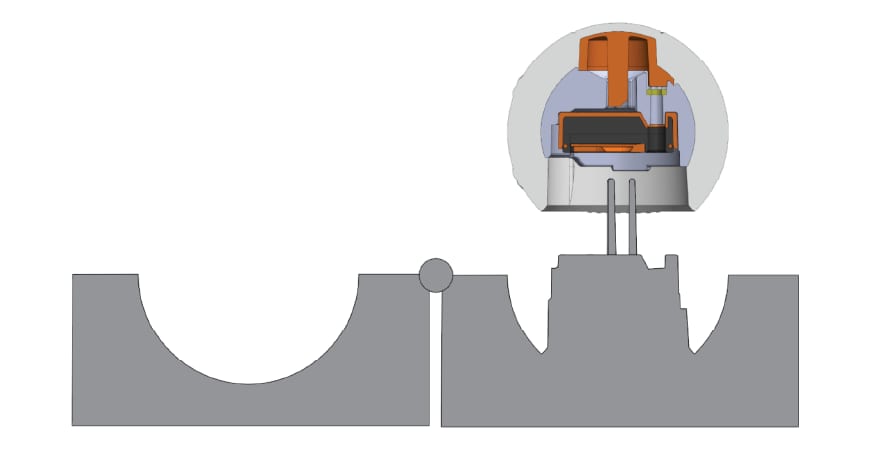
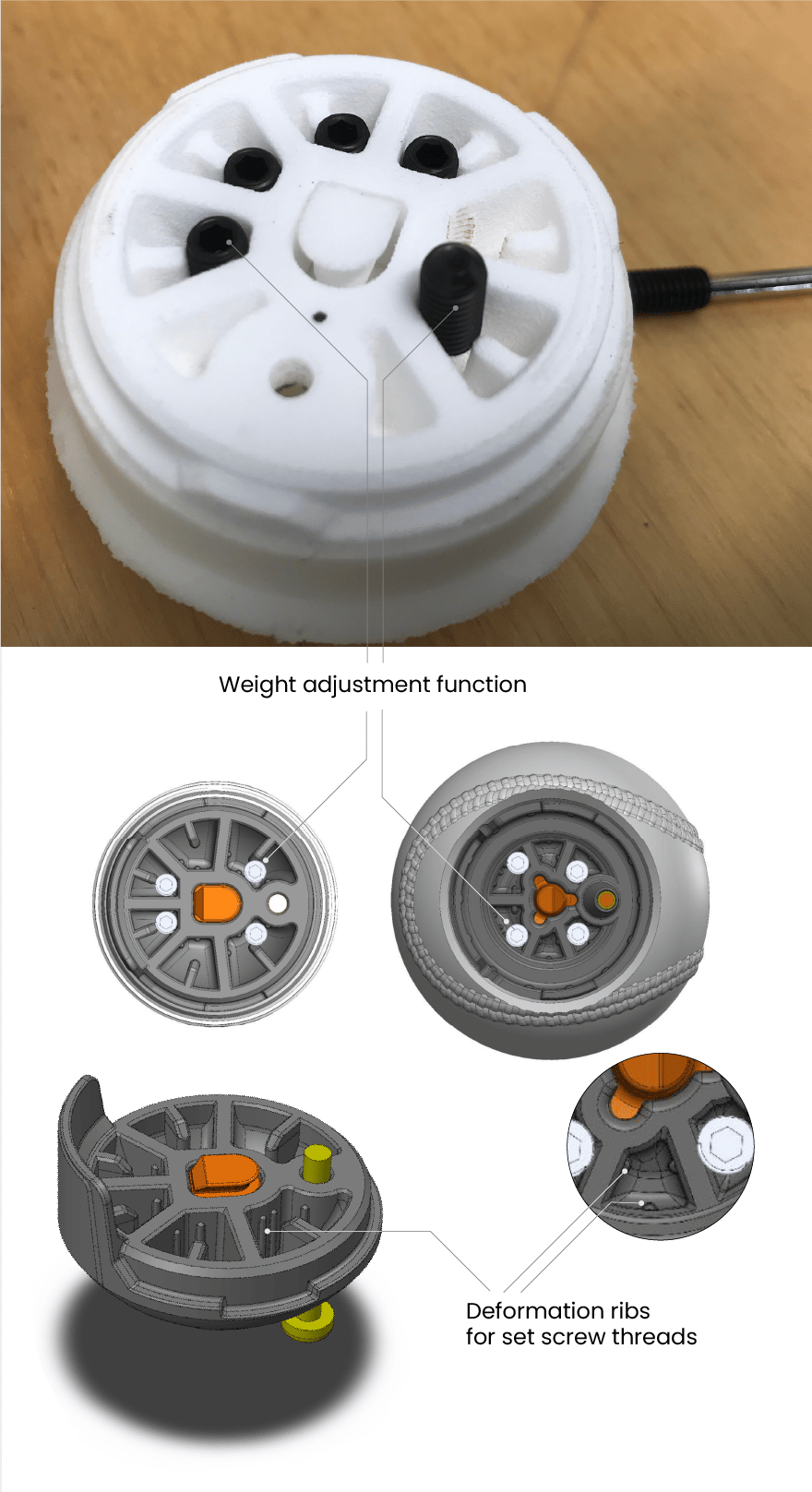
We wanted product to fulfill the standards for regulation baseballs. To hit this weight tolerance demanded a close control on weight management during the engineering of the ball. To tackle the varying weight of foam, I designed a system for adding set screws to core. This gave us a window of 16g for end user to adjust his product to regulation weight.
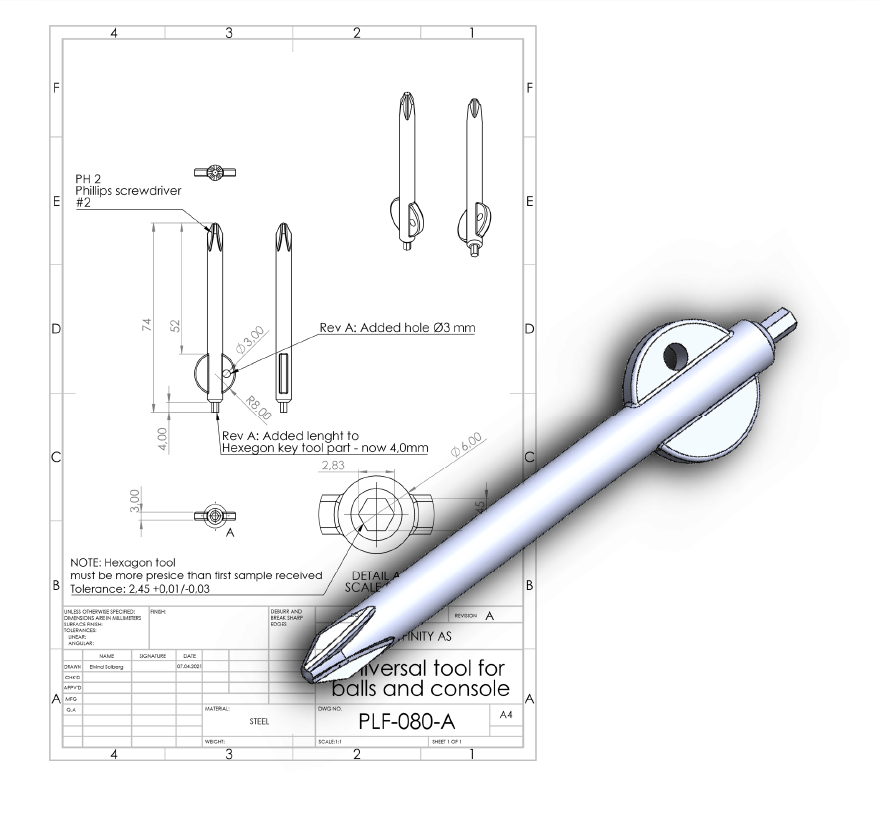
The baseball craved that you needed a hex-key wrench and a phillips screwdriver. To supply that for user in package, and still keep costs low, I ended up designing a costume tool for the baseball product, providing both fastening functions. Finding supplier and right method/material quality was a task in this process, alongside modelling a unit for optimal use and fitting in package.
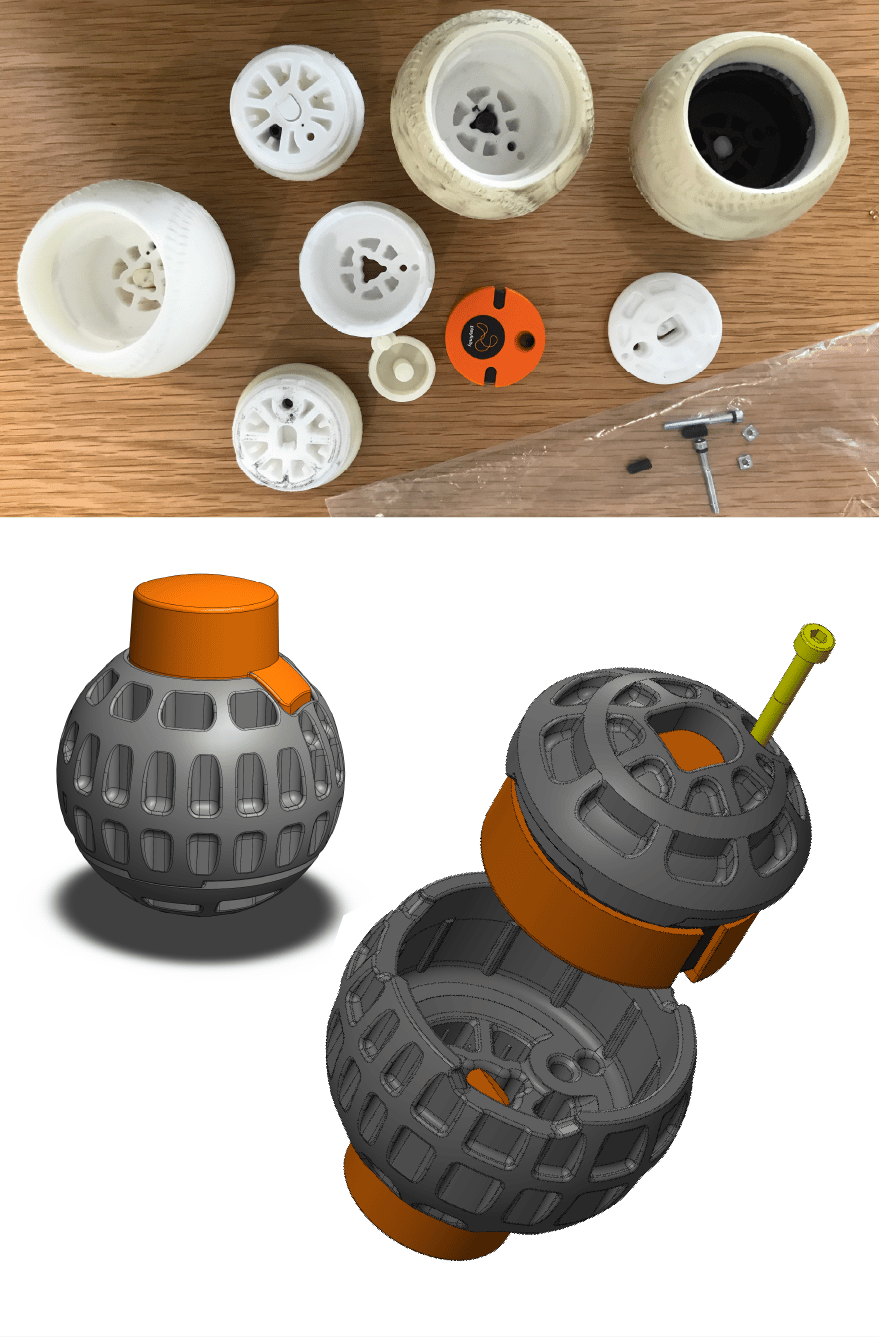
The product being a baseball pitched at high speeds, durability had to have priority. Core construction and functions I dimensioned accordingly. In regards to the molding plastic I had to find the right balance of strength, elasticity and price. I researched alternatives and found 3 plausible choices to investigate further, ABS, ABS+PC and Zytel ST801. Steel quality of screw, as well as printing quality, were elements I had to adjust to get the right durability and quality.
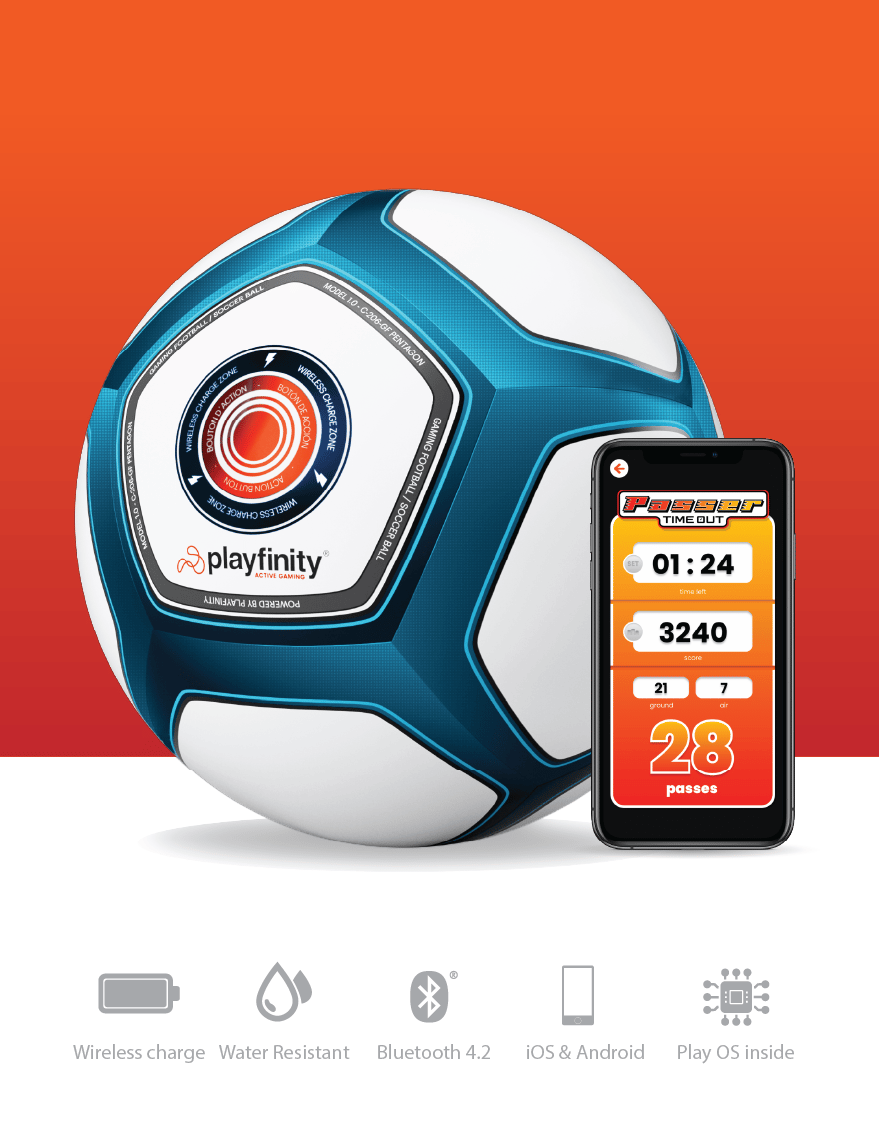
Process: Understanding the possibilities and limitations for production sites. Testing methods and casings for adding tech into various parts of production line. Identify best solution for integration of tech, and developing a system for obtaining right precision in all steps of the production process.
Production tool: I designed a retrofitting unit that was put into the cooking machines for bladder production. This was milled out of a brass block and polished to get right heat transfer in production while letting go of rubber bladder. Part was screwed together enabling integration of heat resistant magnets for easy retrofitting and for mechanical slide of form securing fit into spherical mold. Markers we milled in form to secure precise placement in cooking mold.
bal assembly: Having bladder with reeses, the following process at ball manufacturer was to make production steps for adding bladder to ball skinn. Here I had to get production team to integrate bladder in ball in a new way to secure both valve and button in right place.
Patent: Registered patent on production method for tech in bladder balls, in PCT process now.
Skill sets: Understanding production, Involving production personnel in approaching innovative problem solving, Developing technology in iterations to fit production possibilities, Engineering for retrofitting of production tooling, Production logistics, Rubber production, Football production
RETROFITTING PRODUCTION
GAMING FOOTBALL
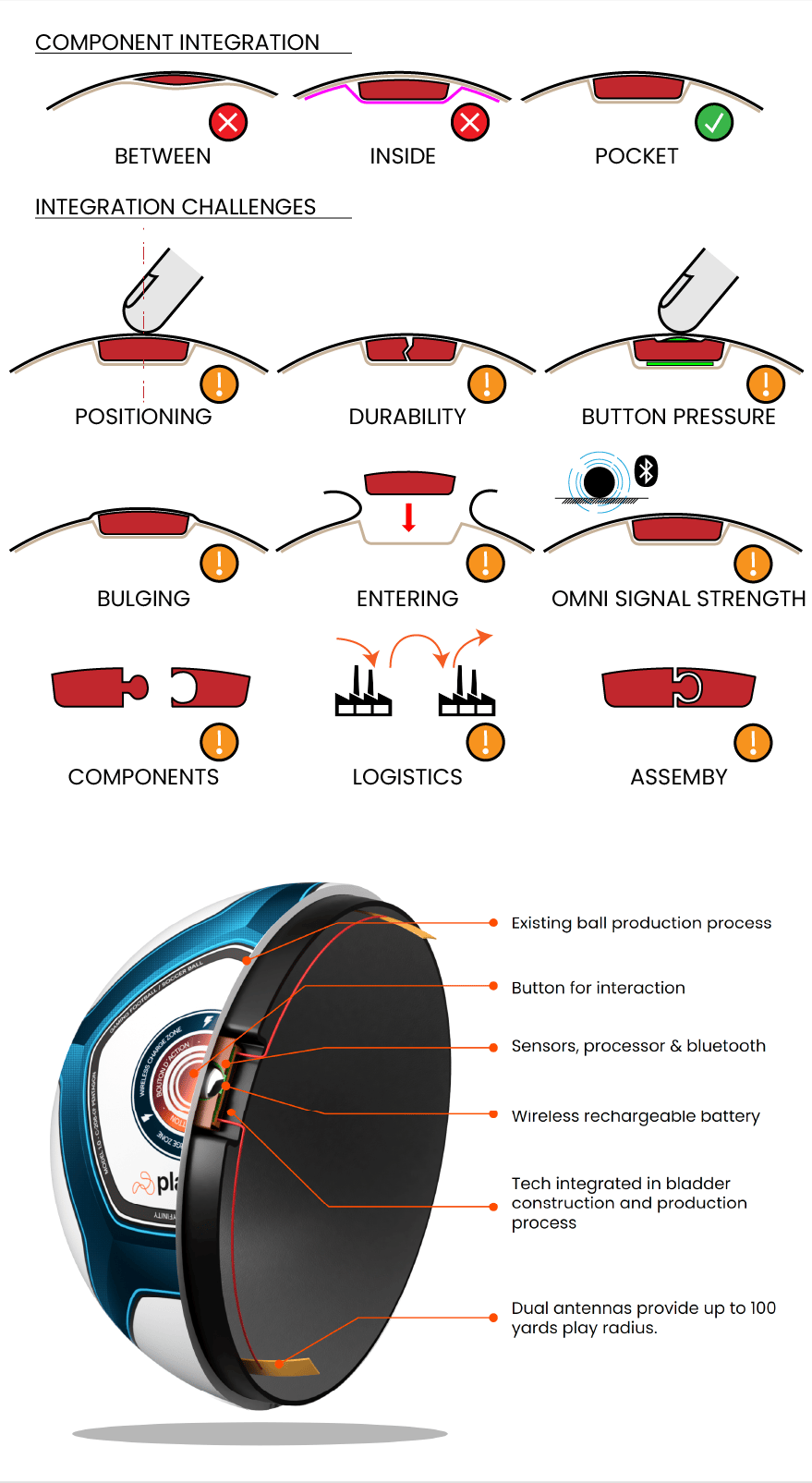
The development process of football was along and challenging. Finding and gaining trust of quality manufacturer for risky innovation project, understanding production possibilities and limitations, convincing production to do new things, finding method for component integration of tech, solving many integration challenges for getting right quality for mass production, getting tech to work in the extreme environment, making assembly of tech production friendly, solving logistics and handling of tech to ball manufacturer. Working with the challenges in a structured way I managed to maneuver the development to result in the world's first ever Gaming Football with a button that performs at match level quality.
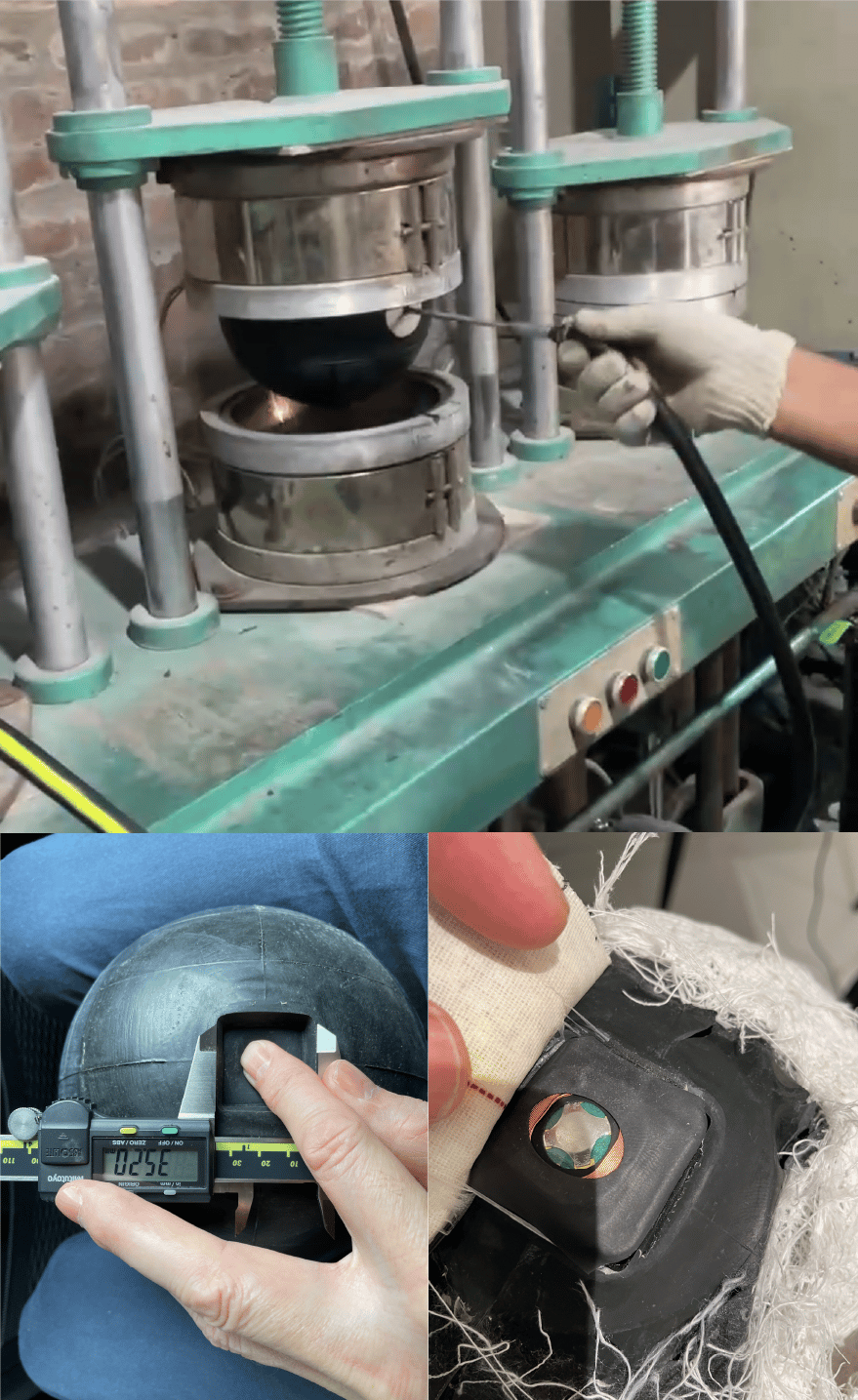
Our Gaming system required a button on the ball (power saving and gaming interaction). This meant we had to put our tech in connection with the ball surface, precisely under the button graphics on ball. The manufacturer thought this impossible, but I worked closely with the various suppliers and workers and developed a method for making this work. Retrofitting the “cooking machine” for bladder with a tool for precise placement of pocket in bladder was a crucial piece in this puzzle. Finalizing the product, the production manager said “you have shown us that anything can be done”. I developed and modelled the system, acquired the components and handled the production of tooling.
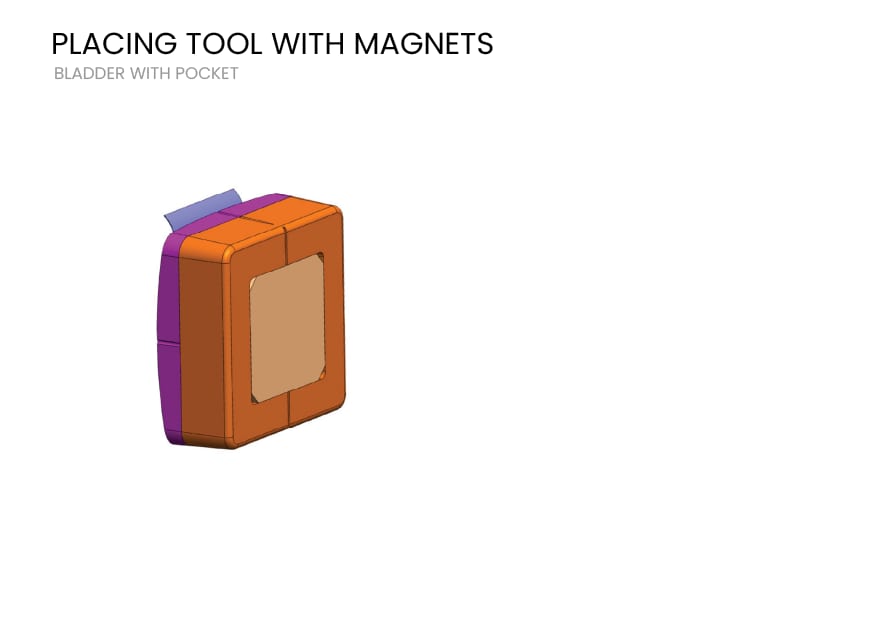
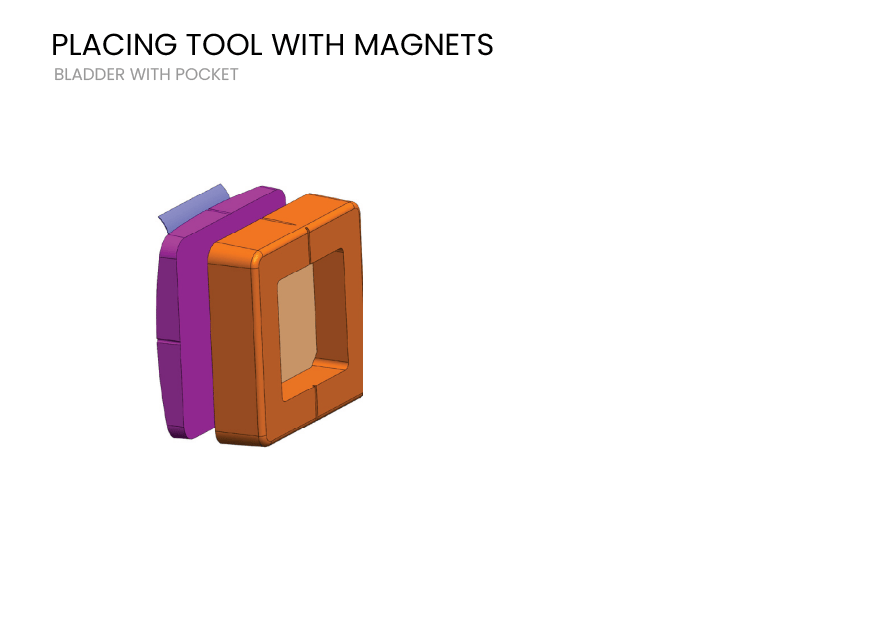
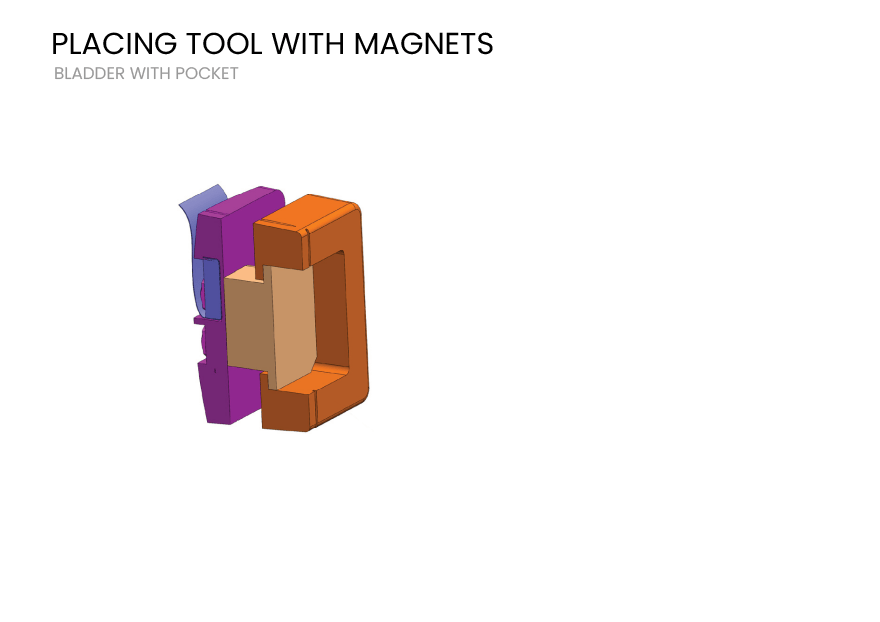
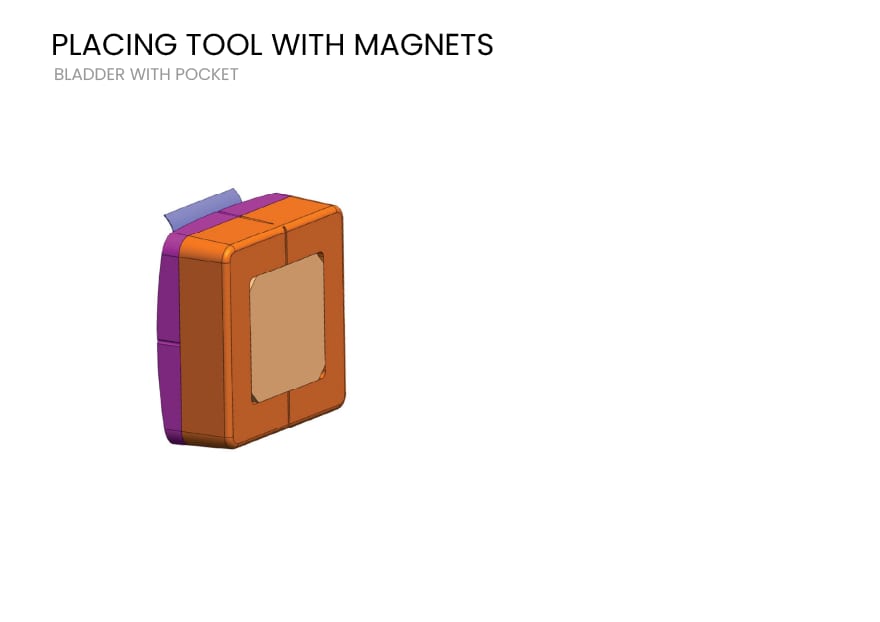
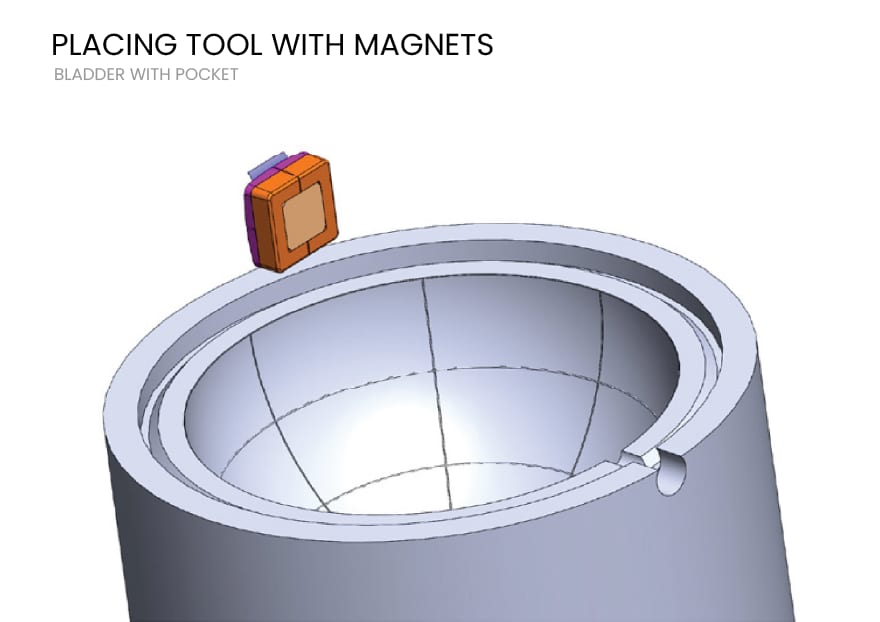
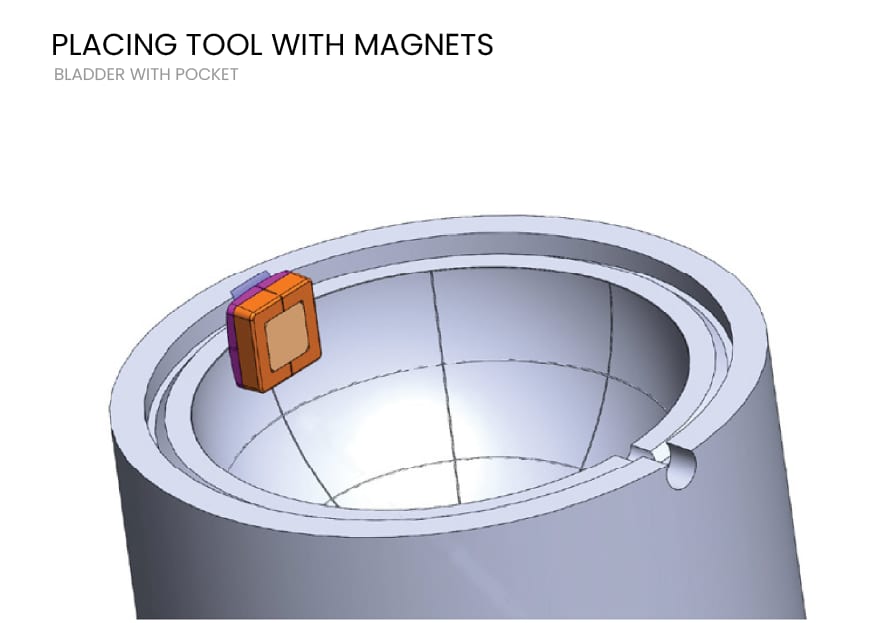
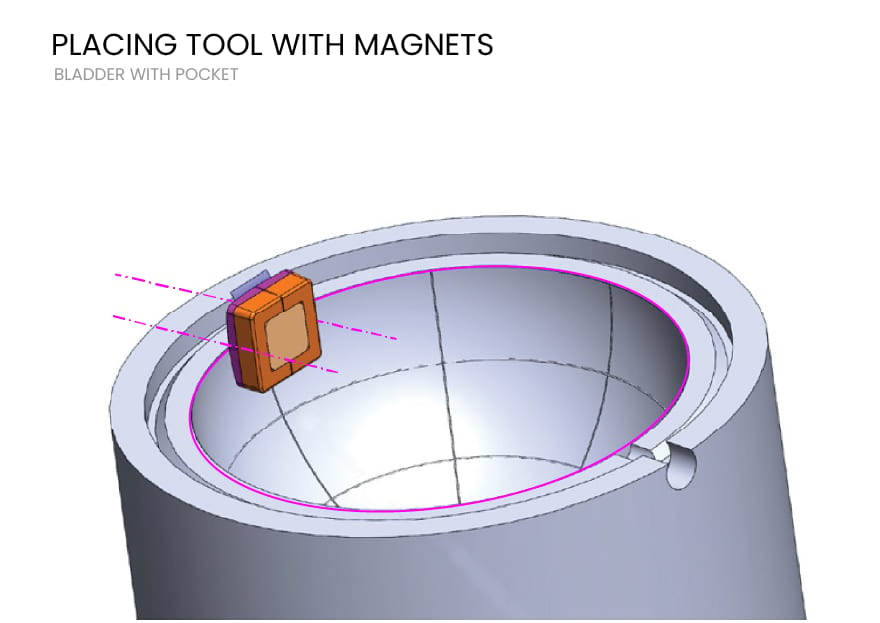
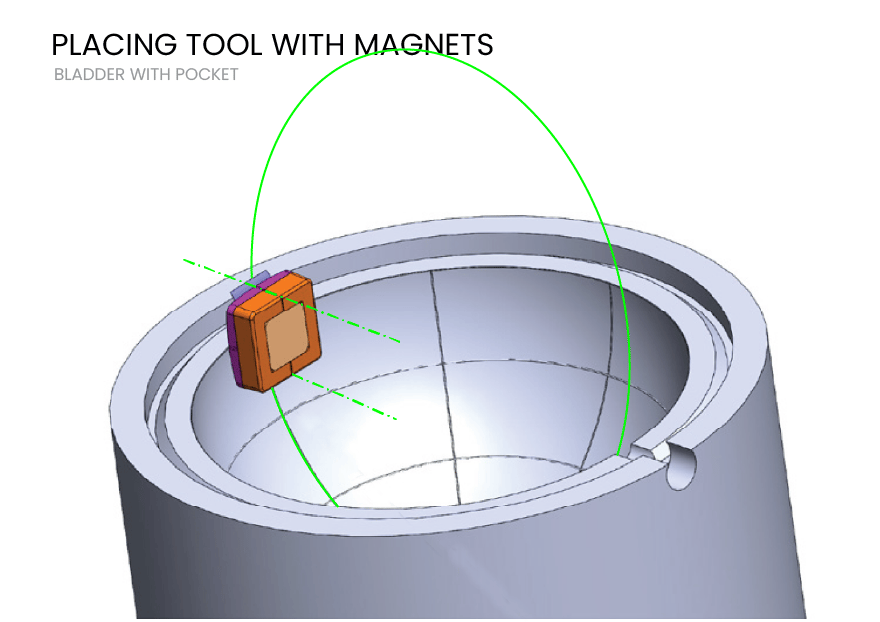
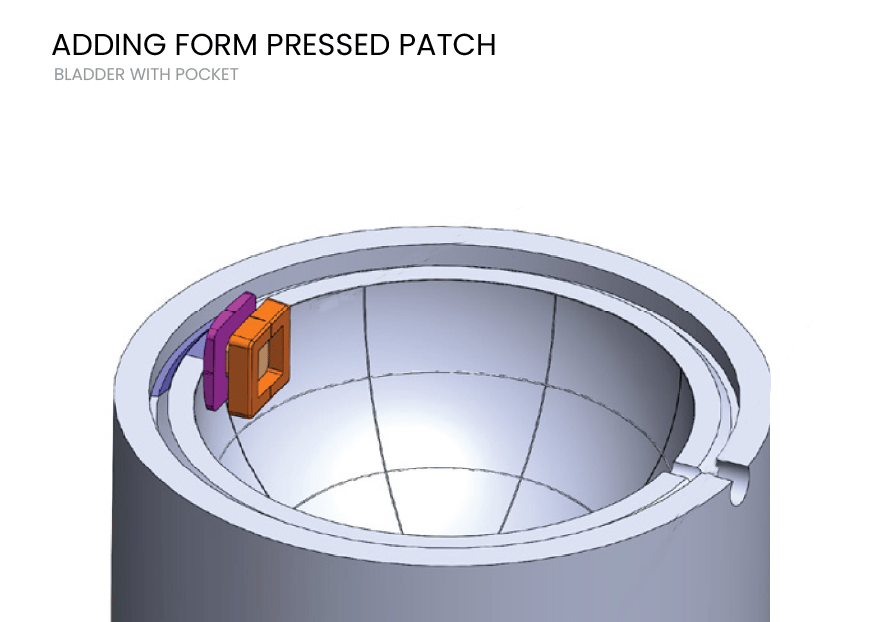
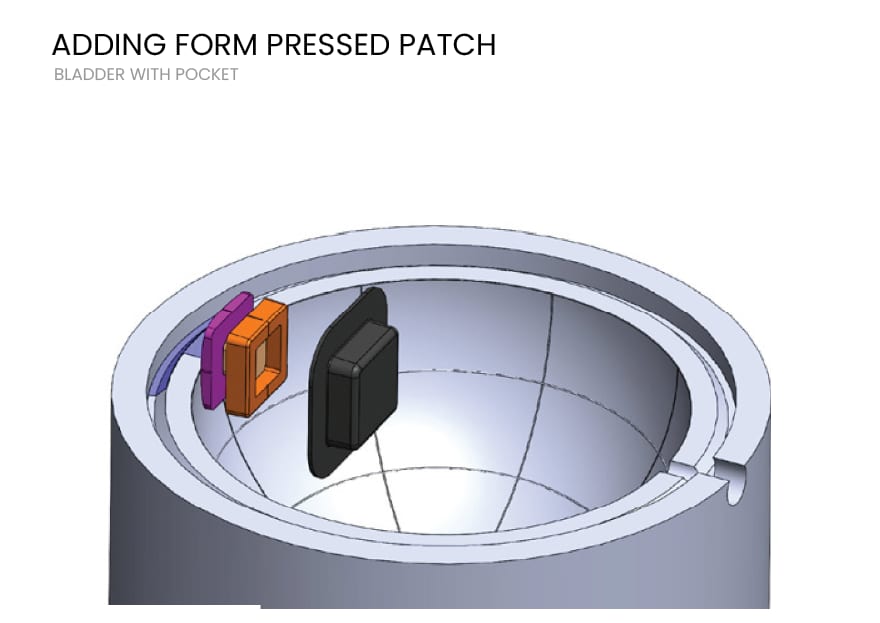
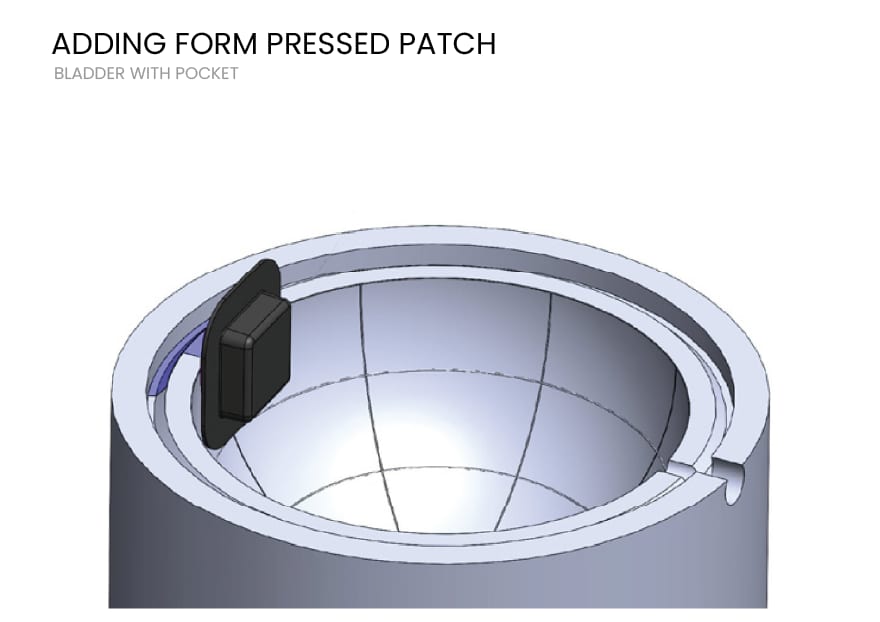
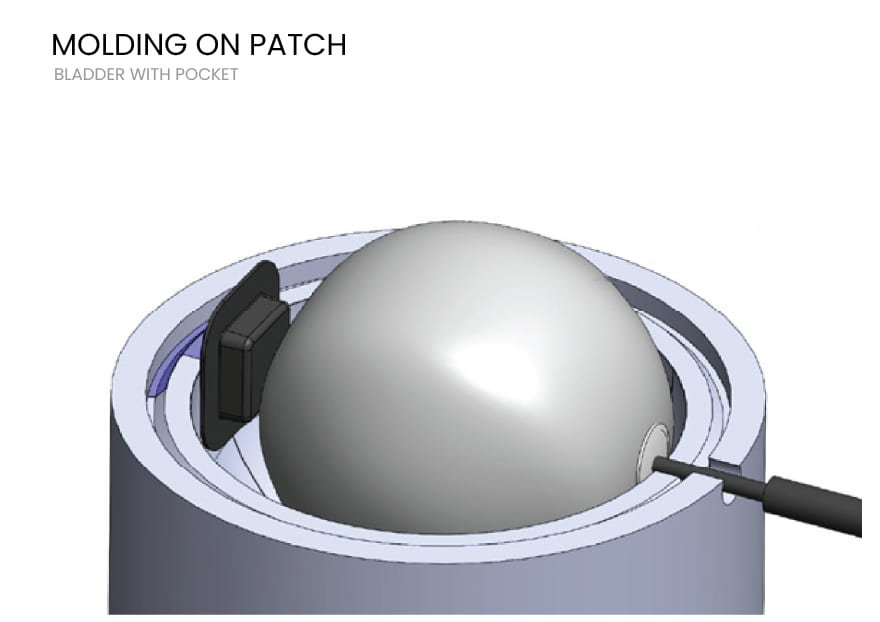
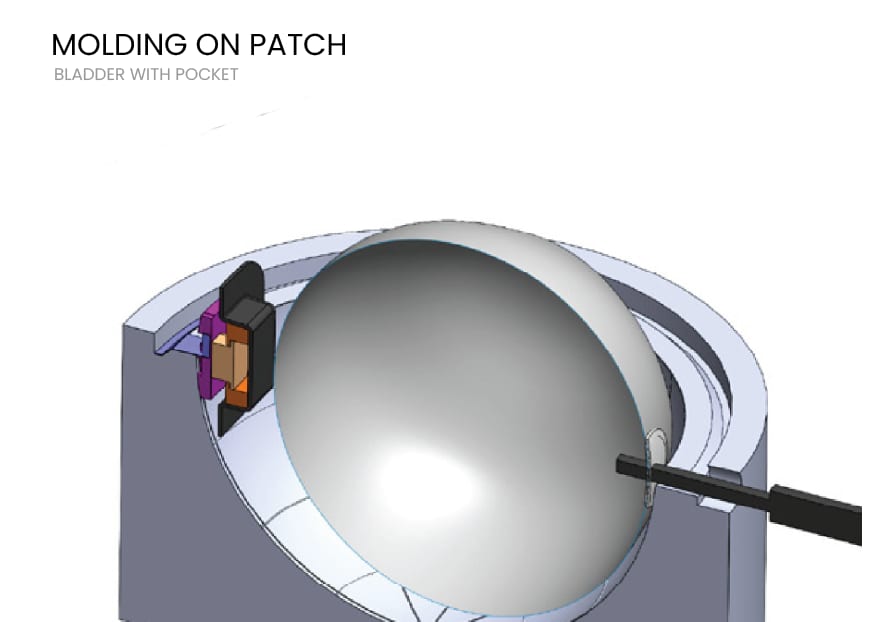
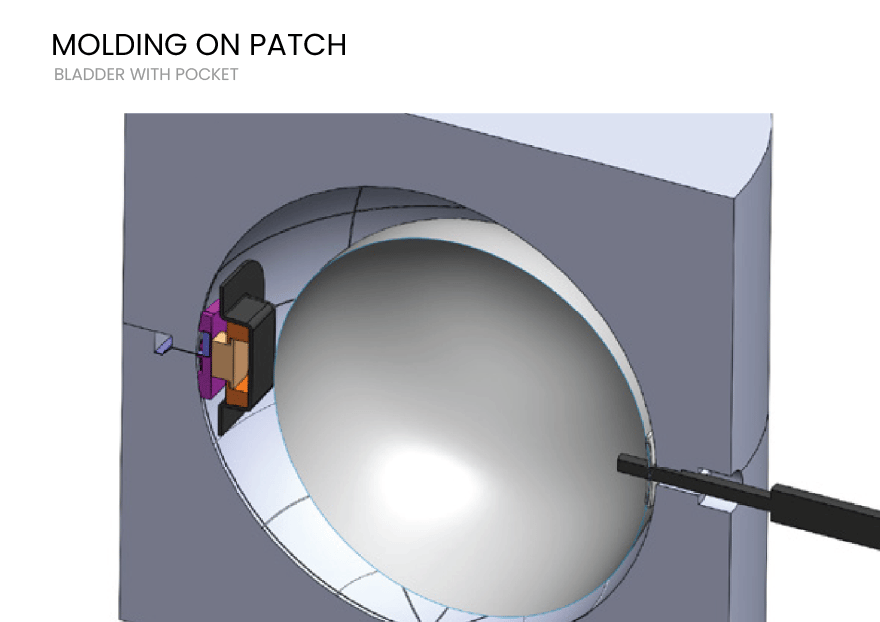
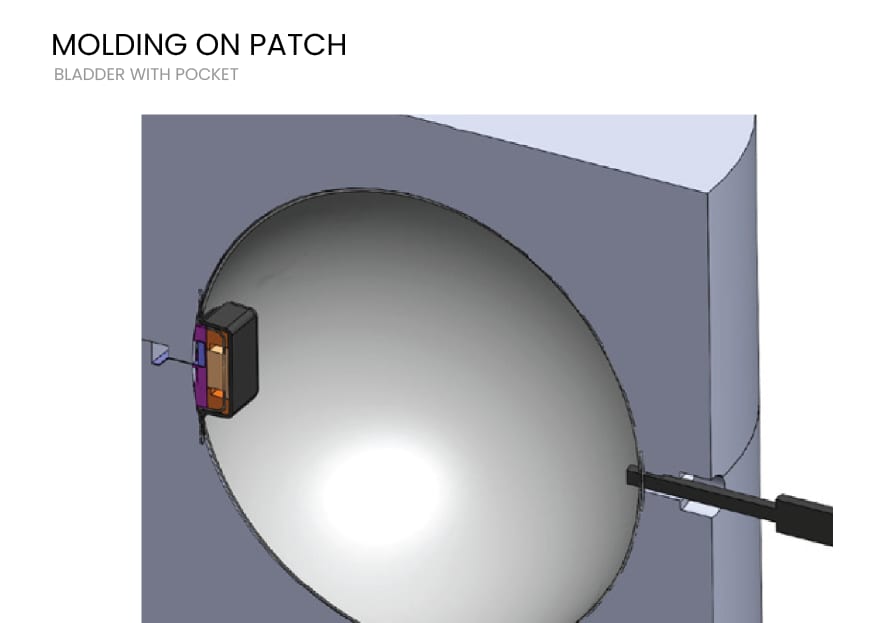
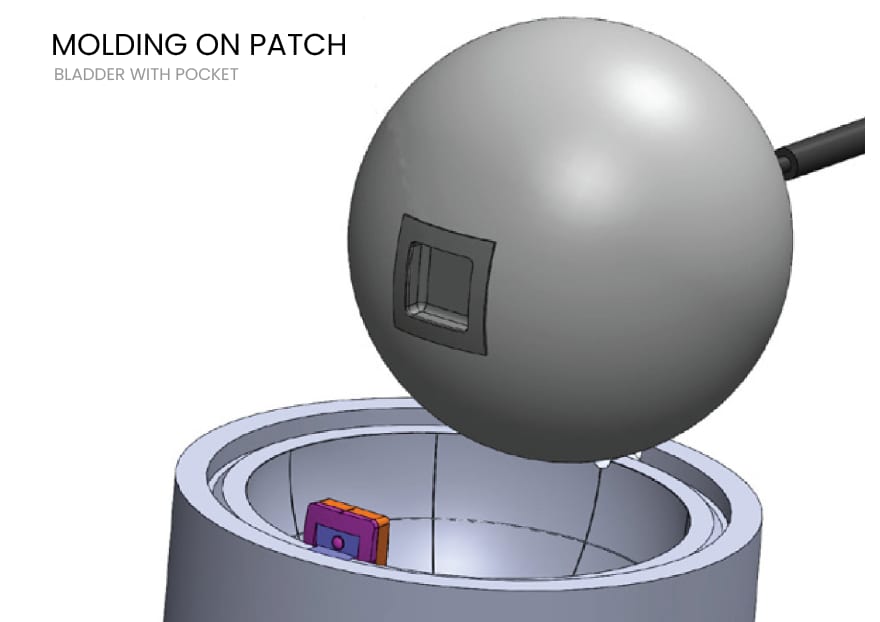
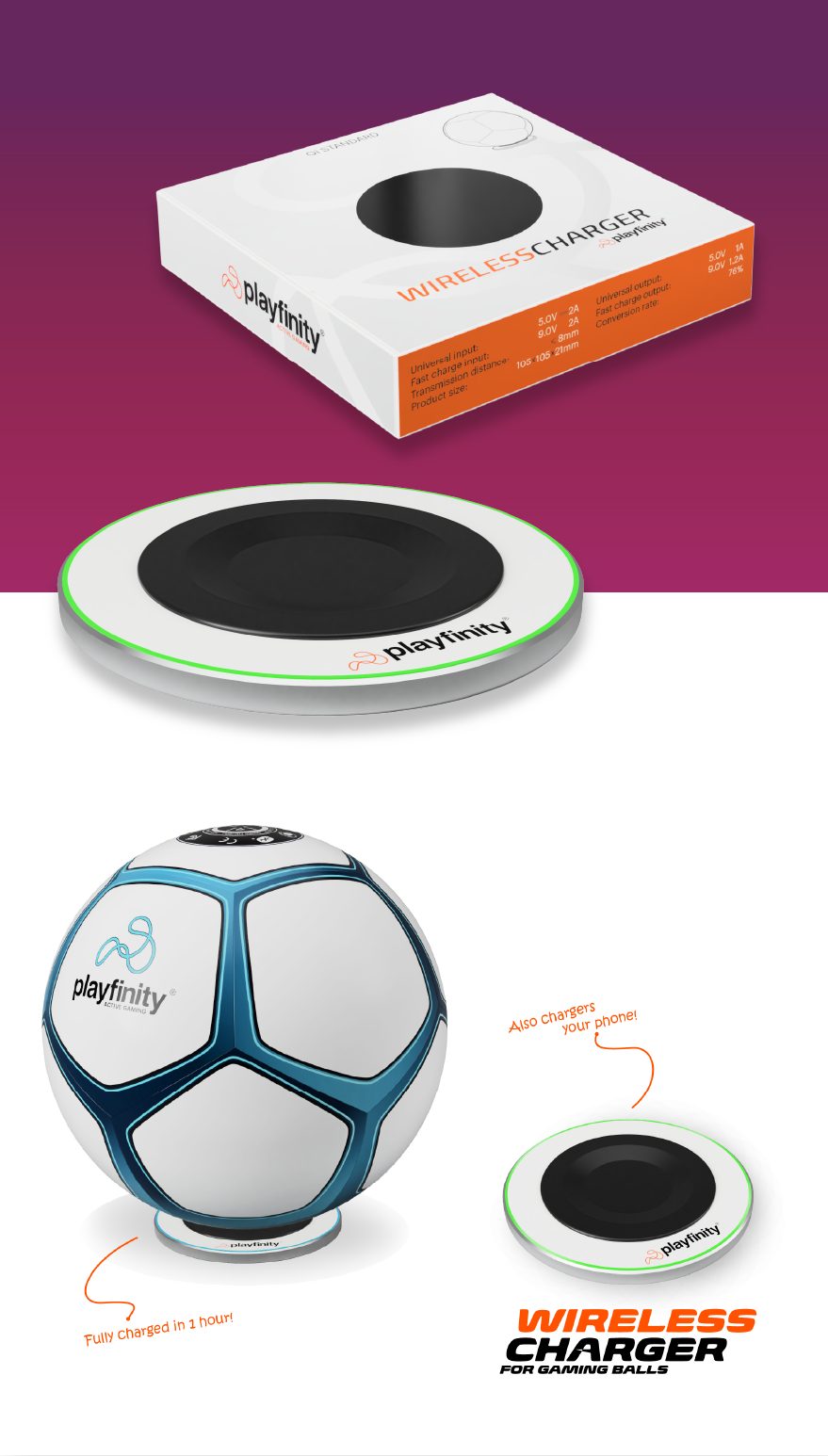
Process: Our gaming football had induction charging. For this we had to find a wireless charger to sell with the product. Via Alibaba we sourced a charger with right quality and price. However, our challenge was that the charging coil was deep into the football, making distance to wireless charger an issue as well as the ball rolling off the charge plate.
The solution was to reengineer that charge plate. I analysed the existing wireless charger product and made various changes, adding a hole to the plastic top casing, and adding a TPR component that would allow the ball to get closer to the charge coil as well as support the ball to balance on charger. I also had the supplier change direction of the coil and adjusted the Ferrit reflector below to optimize the charging.
In the process we also redefined the packaging to optimize size for fitting into new football package.
Skill sets: Reengineering construction, Analysing tech, Communication with chinese suppliers, Rebranding white label product
SOURCING AND ADJUSTING TECH
WIRELESS CHARGER
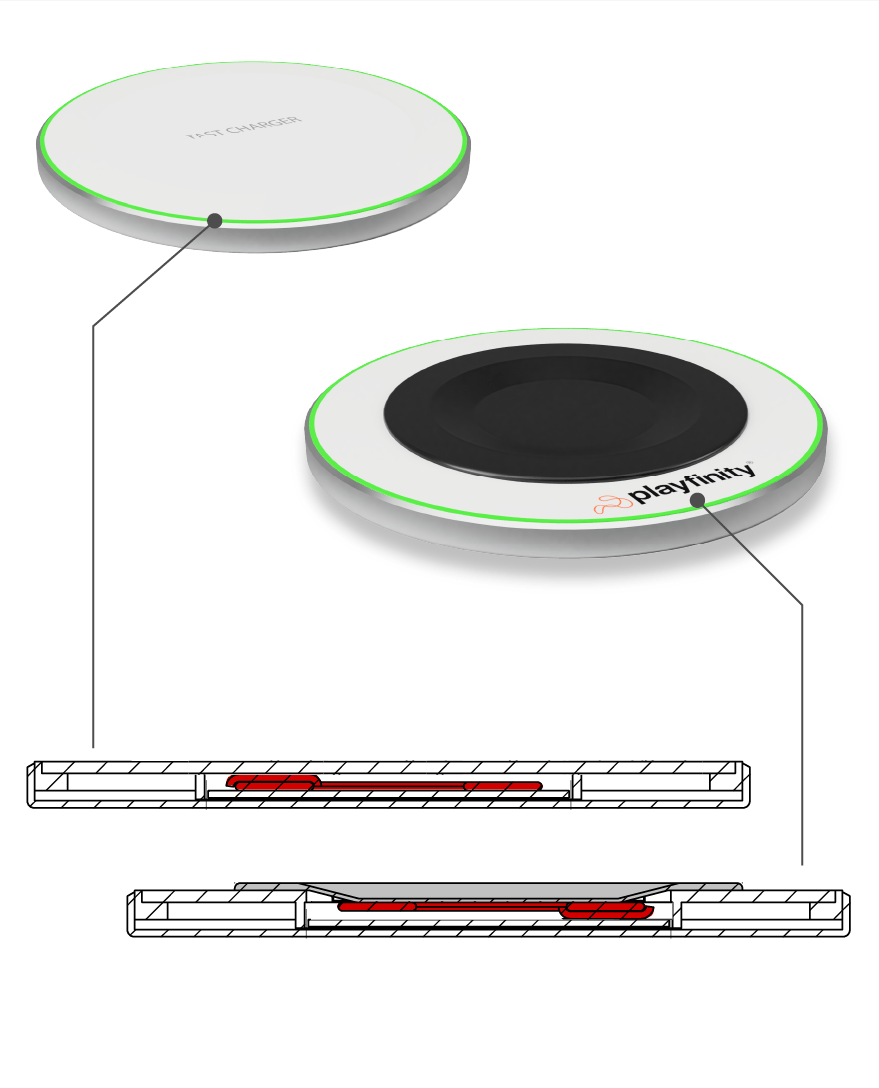
Adding TPR component to charger to balance ball on charger and to minimize distance between charge antennas for induction charging. I also switched direction for the charge coil in wireless charger to minimize distance for charging.
As our charge antenna was deep inside a football, the charging distance was a great challenge. As well as modifying the wireless charger, we had to optimize parameters for charging firmware in football sensor to align with large distance. To be able to see if we were tuning the firmware correctly, I derived a method for testing the results simulating the environment the tech should work in. Using this setup, we could adjust pressure on charge antenna toward football skinn and thus see when the charge would engage. This would give us a delicate measuring tool for detecting if tuning was moving in the right direction.
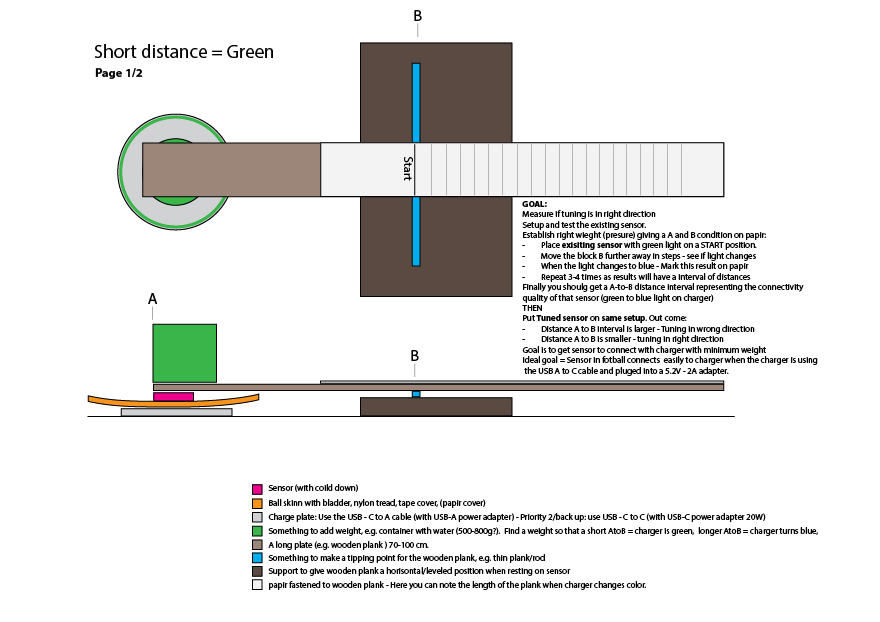
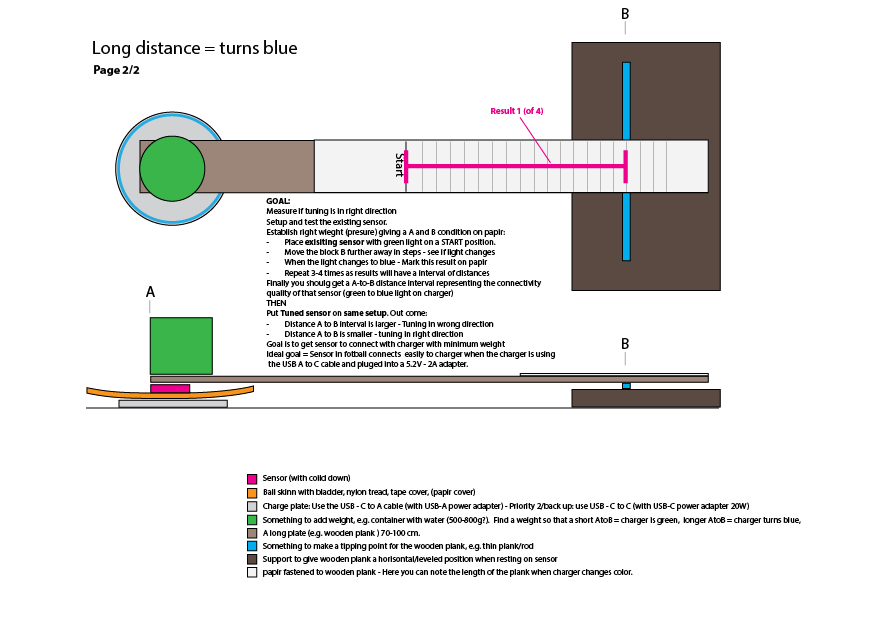
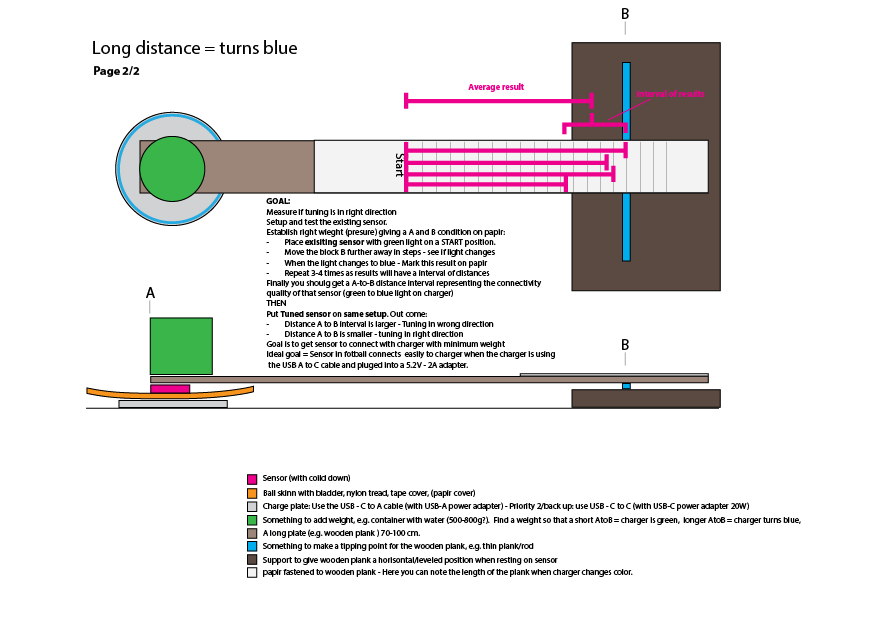
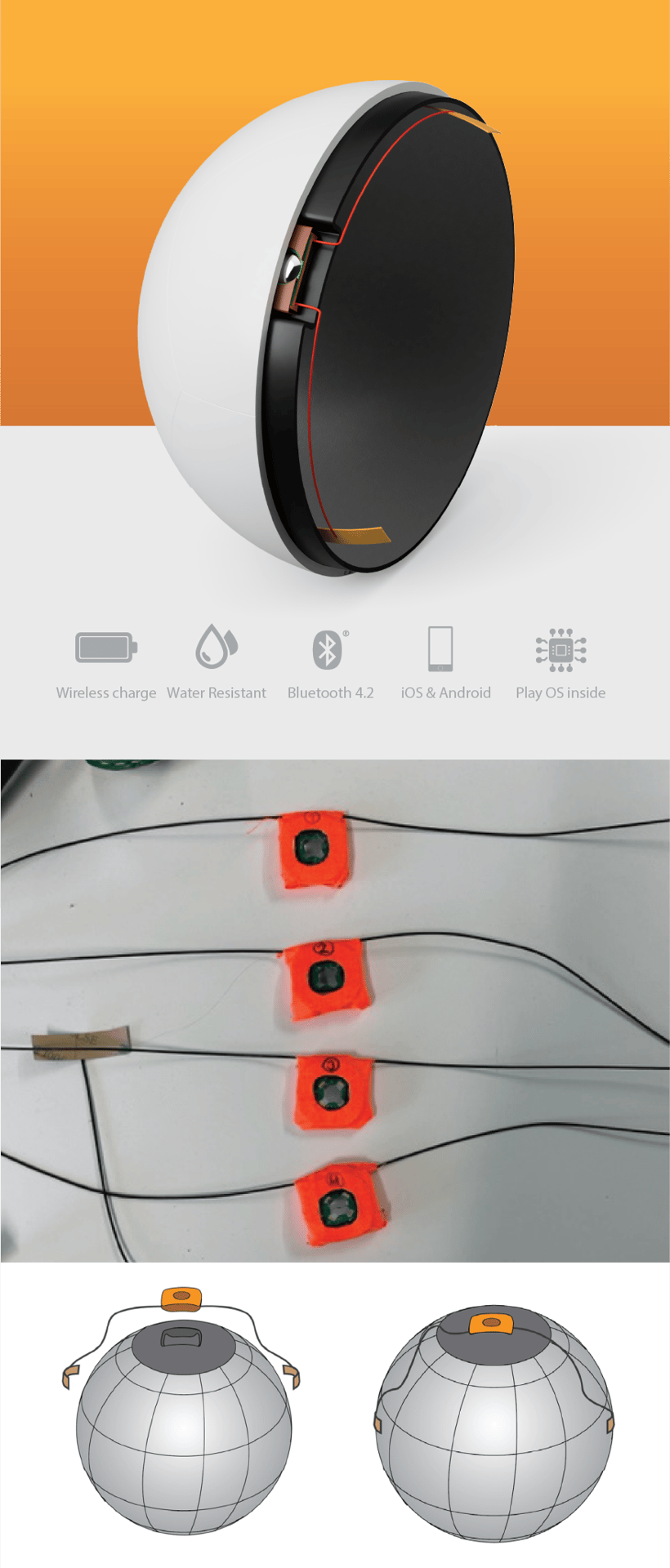
Process: I used a long time to find the right configuration of components with a casing in the gaming football to get right functionality for button and charging whilst protecting the tech from impacts. This also required defining an assembly at tech manufacturer that was optimal for mass production.
Tech components: First steps were to source a variation of tech components to our PCB setup and test the performance. We customized a charge coil to add a hole in the middle, allowing button to be placed in middle. We tested a variation of buttons to get right tactical feedback, and sound through the football skinn, ending up with a dome button solution. I did various testing of constructions to enhance the button functionality so that the user could use his foot to press the button as well. To optimize connectivity we added a dual antenna solution, placing a piezoelectric/flexible antenna at each side of ball to always have height over ground - optimizing connection range. Testing revealed that the lithium battery needed a firm wall protection to avoid deformation.
Casing: Having the right combination of components, the task was to create a casing and assembly that provided good production flow and gave right balance between protecting tech and not creating a hard element to ball surface. The solution being choosing a suitable type of football production (Hybrid ball) and making the casing from 60 shore silicone.
Challenge: Developing the tech casing was very challenging as every iteration had to undergo a prototype production in France/tunisia first, then get transported to pakistan for ball integration, and lastly to Norway for testing. Once in ball, we could not access the tech without destroying the ball. Hence, we had to go about very analytic and structured to deduct the findings from each iteration. It was also extremely time consuming.
Skill sets: Co-developing technology, Production optimizing for technology, Handling BOM foundation, Collaborating with print circuit designer, prototyping tech, coordinating multiple suppliers
TECHNOLOGY DEVELOPMENT
TESTING & PRODUCTION
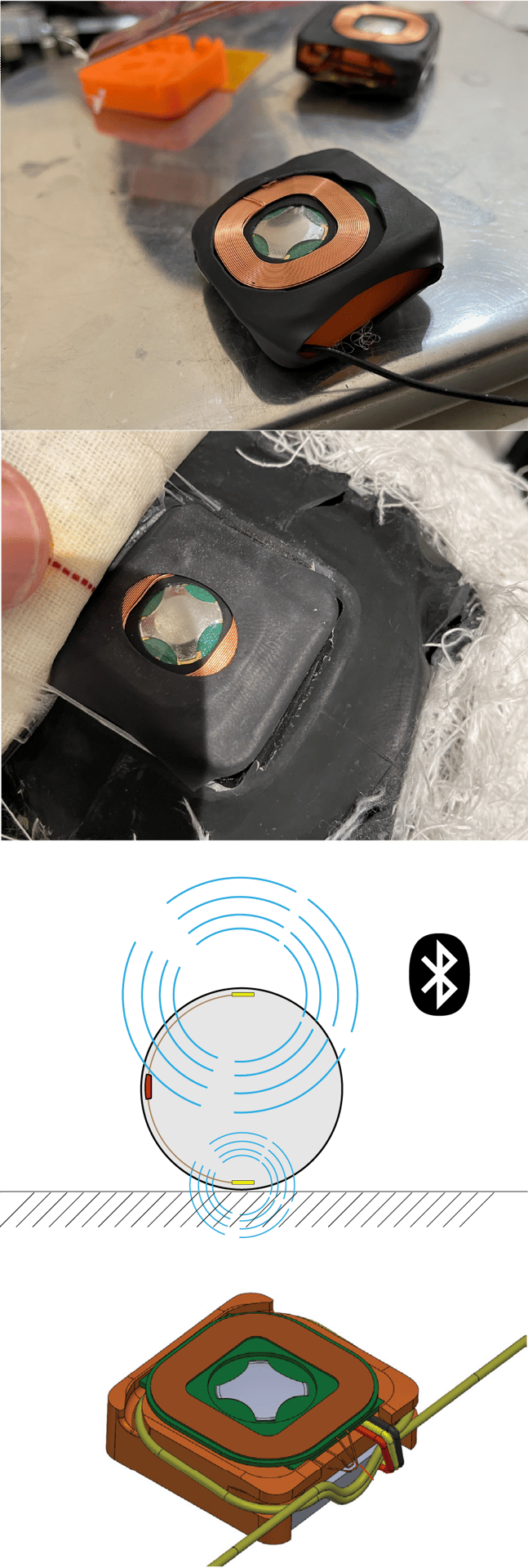
A major challenge was deciding on tech components, configuring them and making a production process that was mass production friendly. Many iterations and tests were performed to get the right functionality. I ended up with a press molded silicone part that assisted a efficient assembly and that gave the optimal positioning and protection to components, whilst flexible enough to not affect bounce and roundness of football. In the process the I convinced my CTO to go for a dual antenna system to avoid losing connectivity with ball. This way we would always have a antenna sufficiently off the grown to maintain long distance connection.
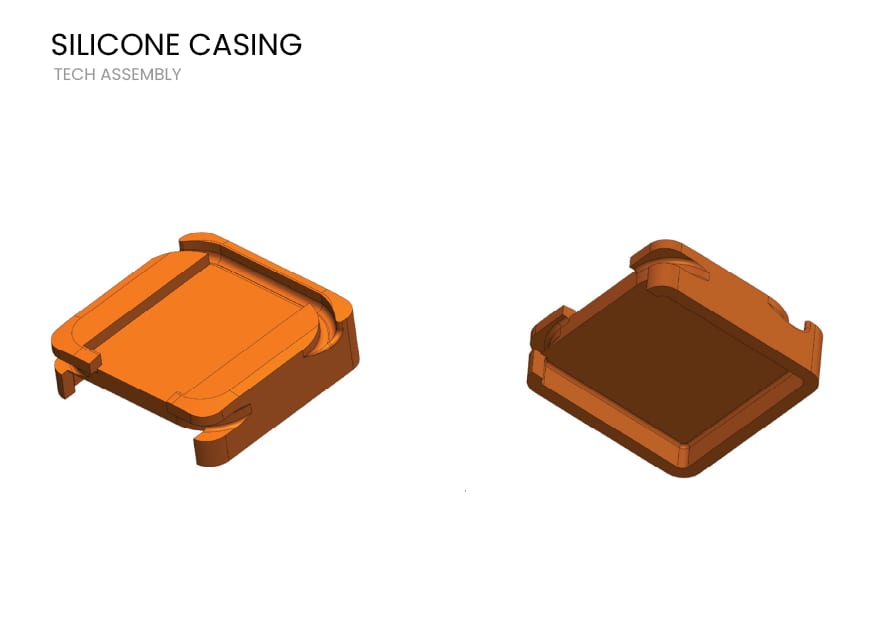
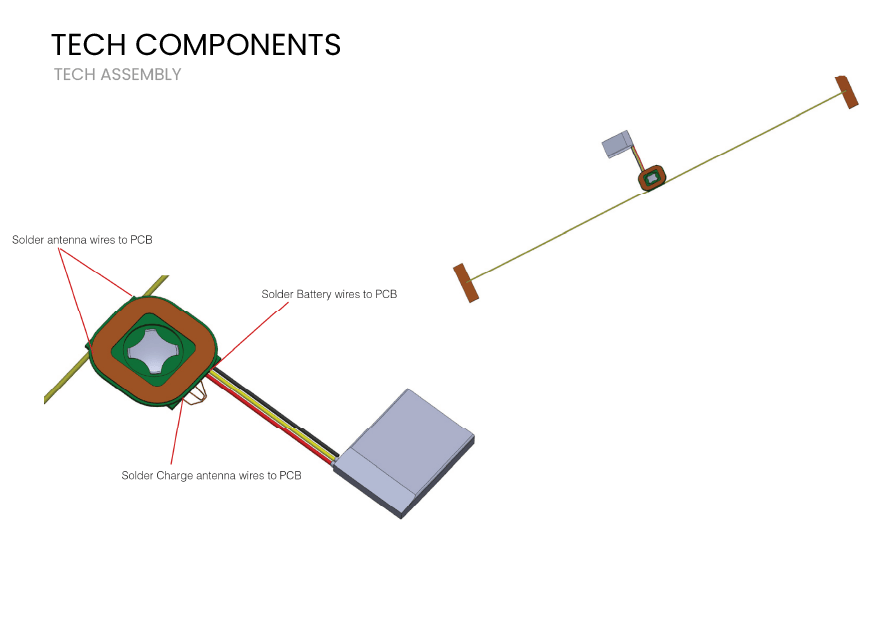
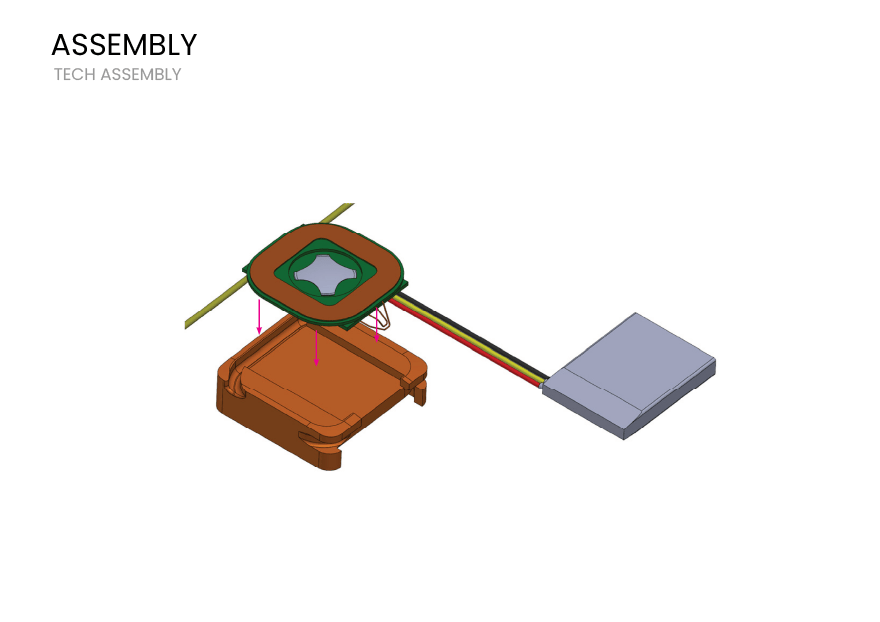
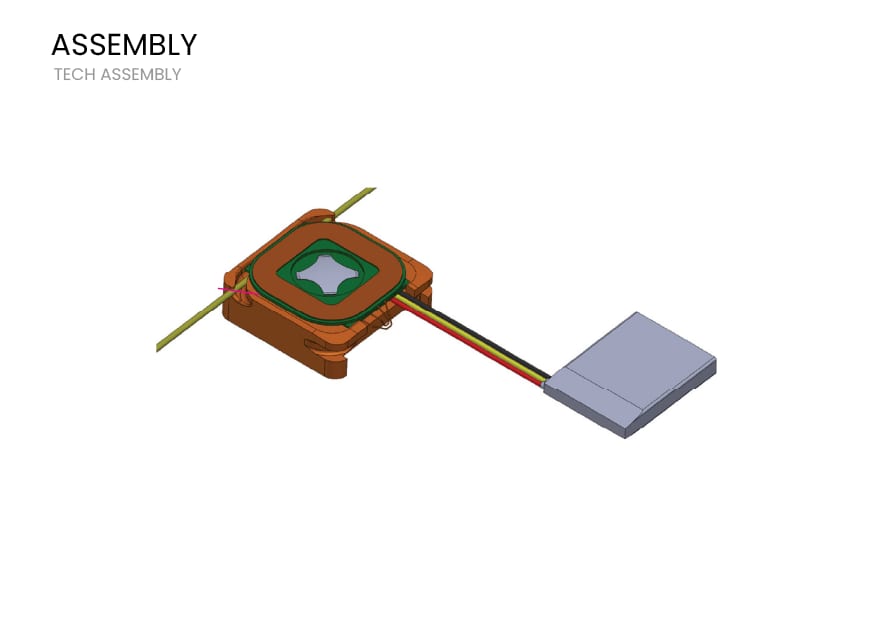
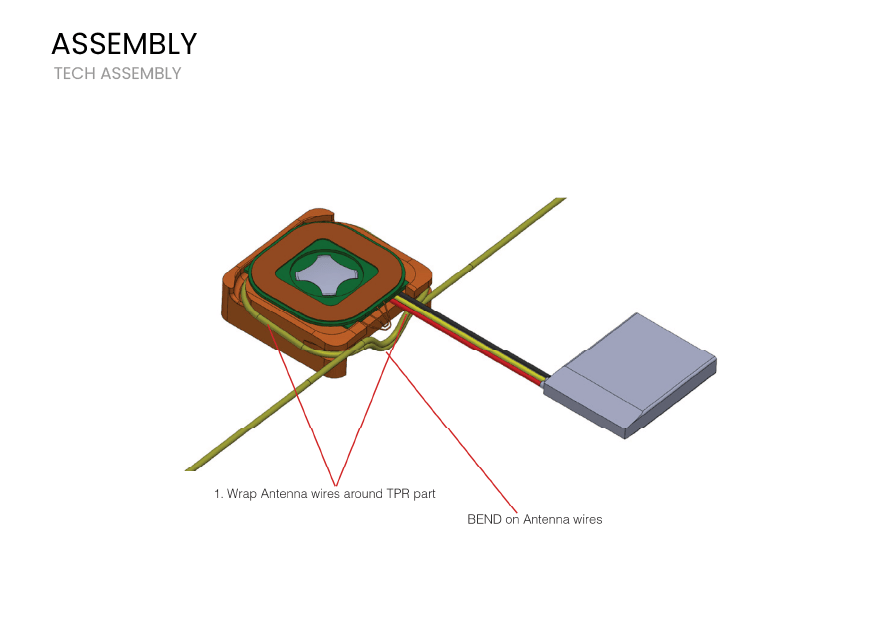
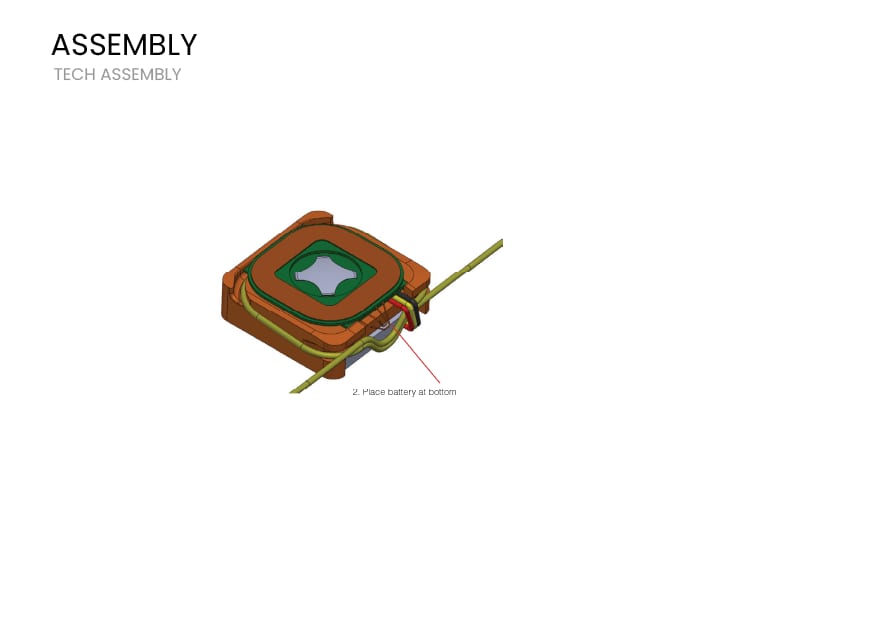
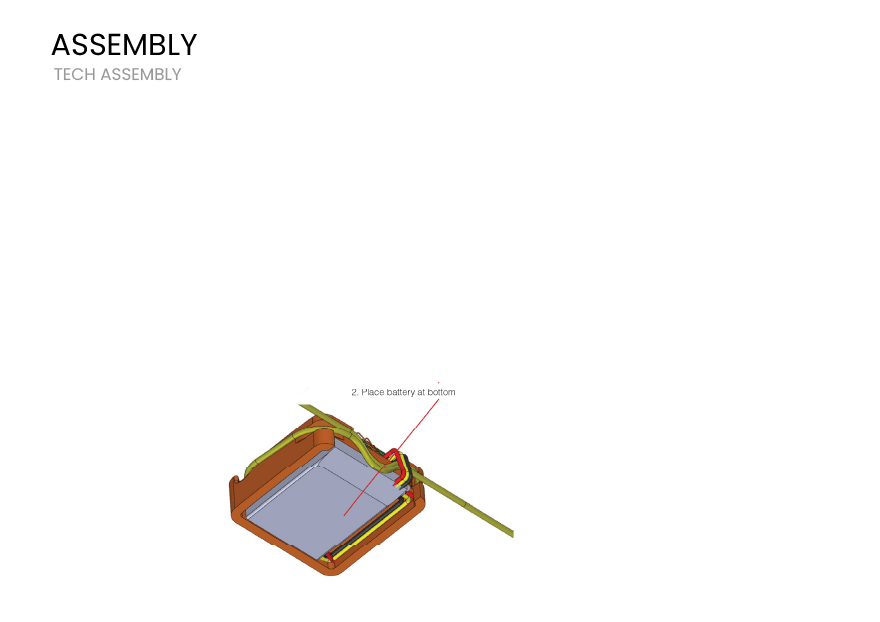
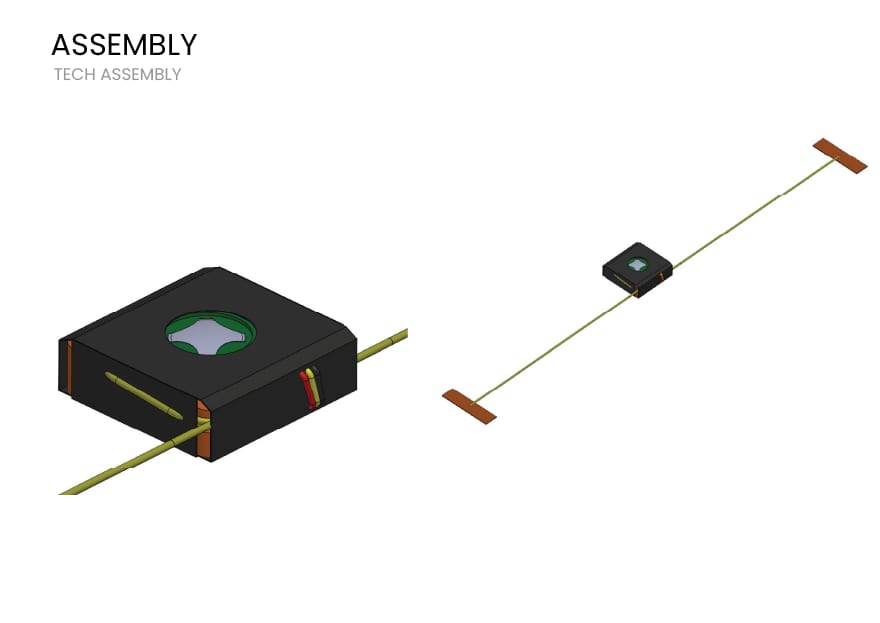
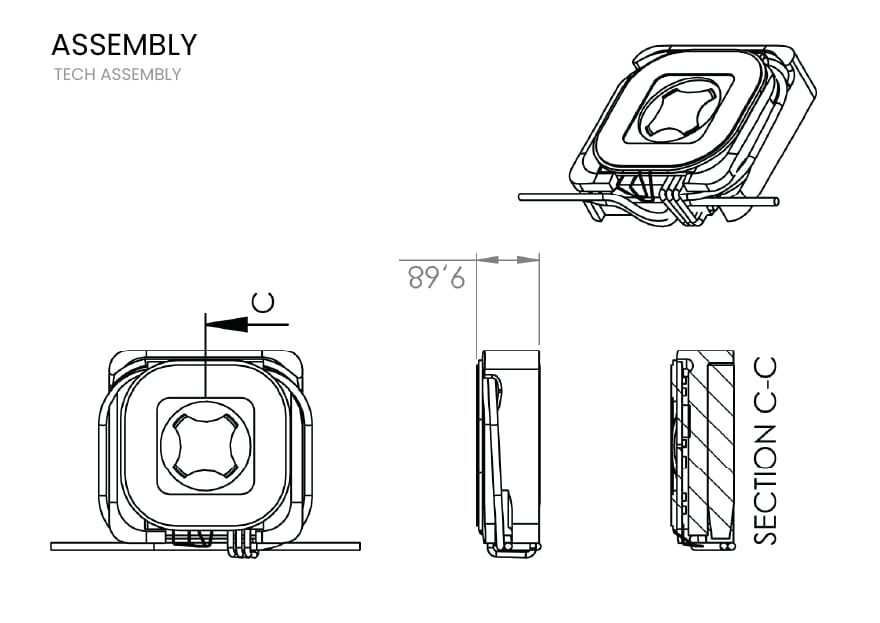
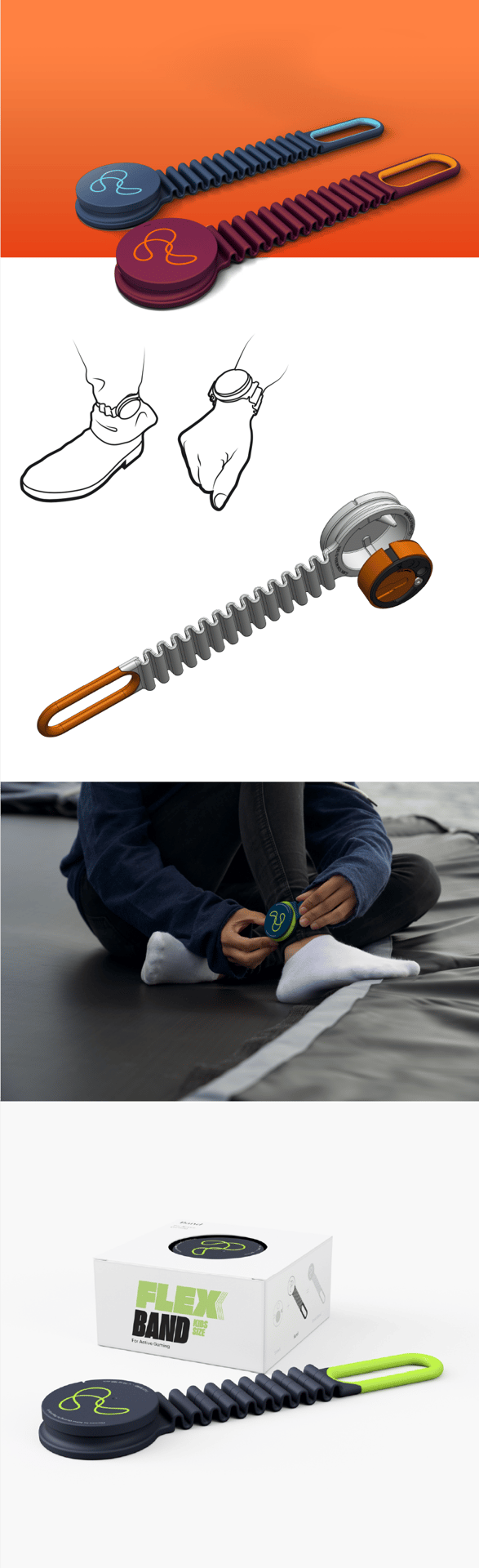
Process: We wanted to make games for trampolines fastening our Activity tracker to the ankle. To do this we wanted a simple robust low cost one size fits all unit that did not have any mechanics that would get worn. The concept became a single flexible silicone band; robust, weather resistant, good friction and works well against direct contact with skin. Using only one material had also a positive environmental aspect for easy recycling.
The challenge: The challenge was designing a flexible object to give the right amount of presume against body to both feel comfortable to wear and still allow sensor unit to remain rigidly in its place. Testing various structures and experimenting with different shore values gave us the right balance between flexibility and stiffness. Making use of the hard structure of the activity tracker allowed us to get a sufficient holding mechanism.
Two component mold: To get a nice material/color contrast in the product, I made the loop part a separate mold process. Having this tampong printed was inconvenient and did not give an aesthetically good result.
Skill sets: Modelling for injection mold with silicone, Investigating silicones for right characteristics, Rapid prototyping, sourcing production facilities, communication with chinese manufacturers, Tampong printing
DESIGN FOR FLEXIBLE CONSTRUCTION
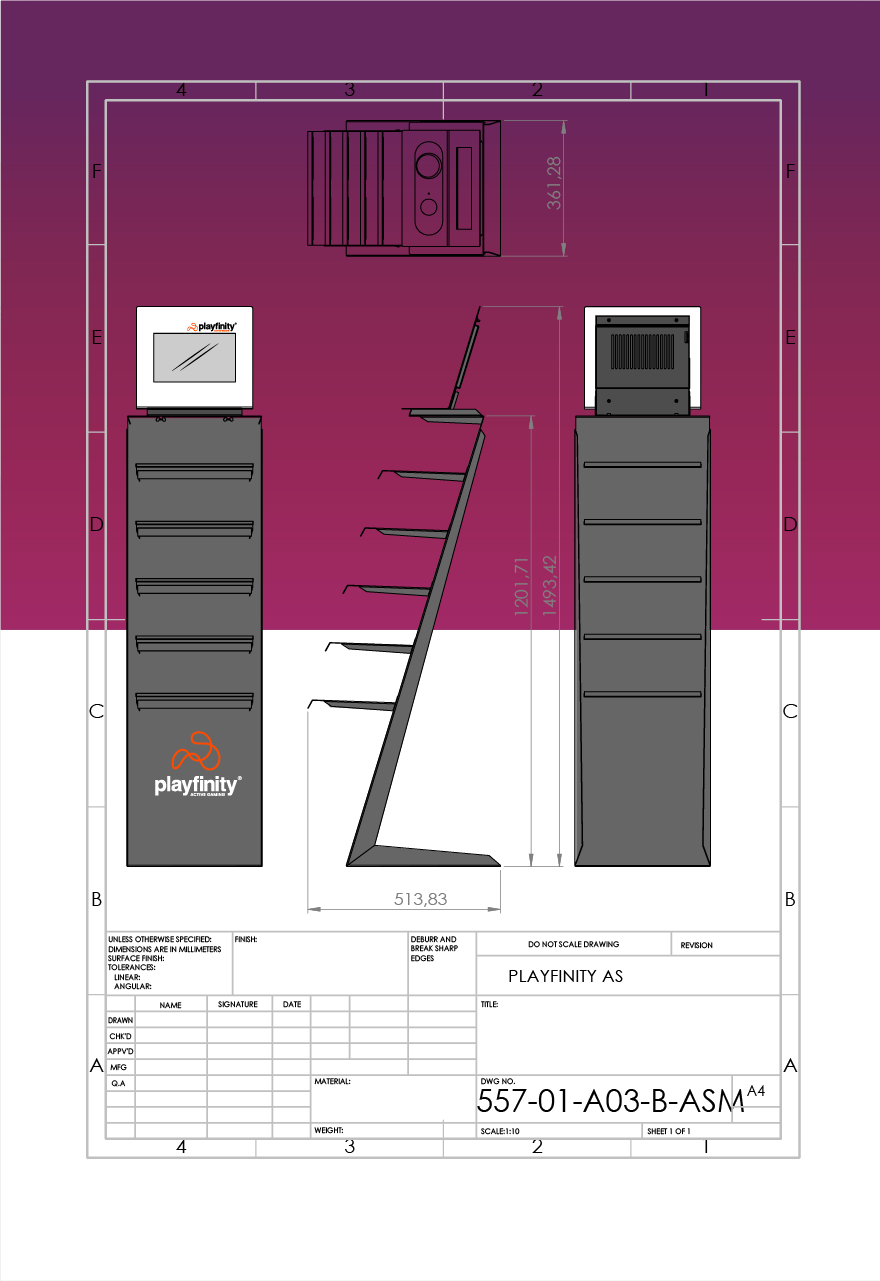
We wanted a stand alone display for our Smartballs and Jumpgames products in stores that had a screen integrated into it, and substantiated a quality text product. This way we could demonstrate the tech products through videos in stores. I made some concepts and landed on a metal sheet construction. This allowed the top part, with screen, to be detached for presentation by cashier. It also had a flexible shelf system to adjust to new, larger packaging down the road.
Skill sets: Modeling for sheet metal construction, Communication towards sheet metal production facilities, Display design
SHEET METAL CONSTRUCTION
PLAYFINITY DISPLAY
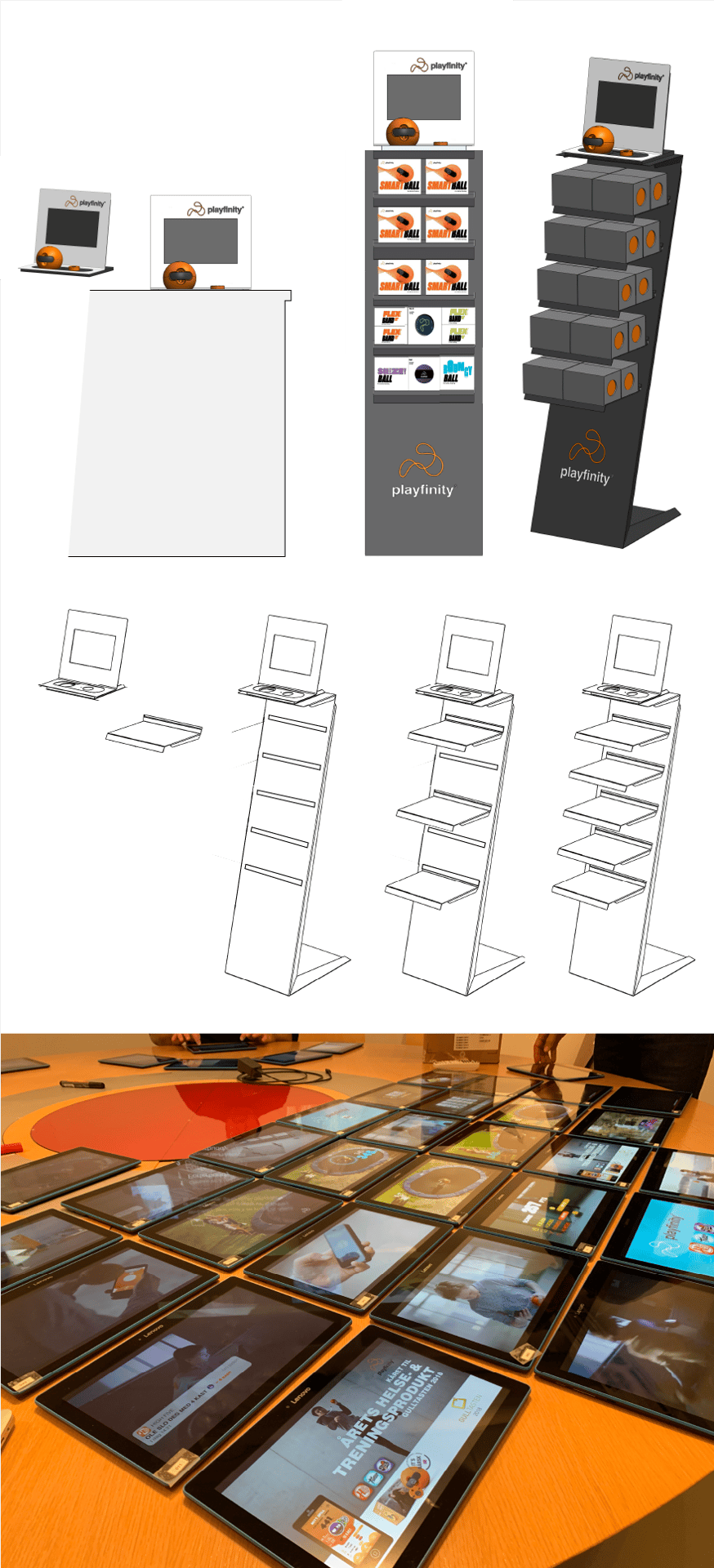
Picture from preparing 50 displays for sales displays in retail. Tested that all displays could be remotely adjusted from out offices.
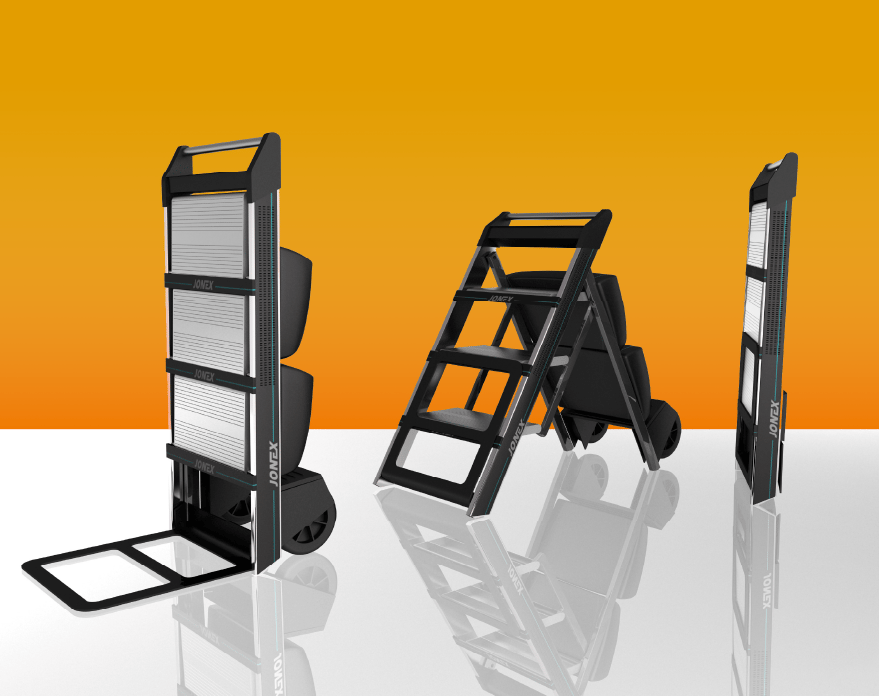
Working with the portable workstation for Grove knutsen as designer at Inventas, I was hired to make a working prototype of the concept. in this process I had to engineer the mechanics so that folding the ladder into a trolley would work smoothly. Using motion mechanics in solid works I could determine the right akses for the folding mechanism. Based on this I had a large aluminium profile made to make the steps work accordingly. I also had to engineer how rest of the product would come together in a production friendly matter, including injection molded parts.
Learning: On important learning from this project was that you should hurry slowly, and always make simple physical prototypes of whatever you are making. Shortcuts never gain you in the long run, especially when dealing with mechanics.
Skill sets: Construction with aluminum profiles, Advanced mechanics, Assembly for aluminium structures, Prototyping
ALUMINUM PROFILES & MECHANISMS
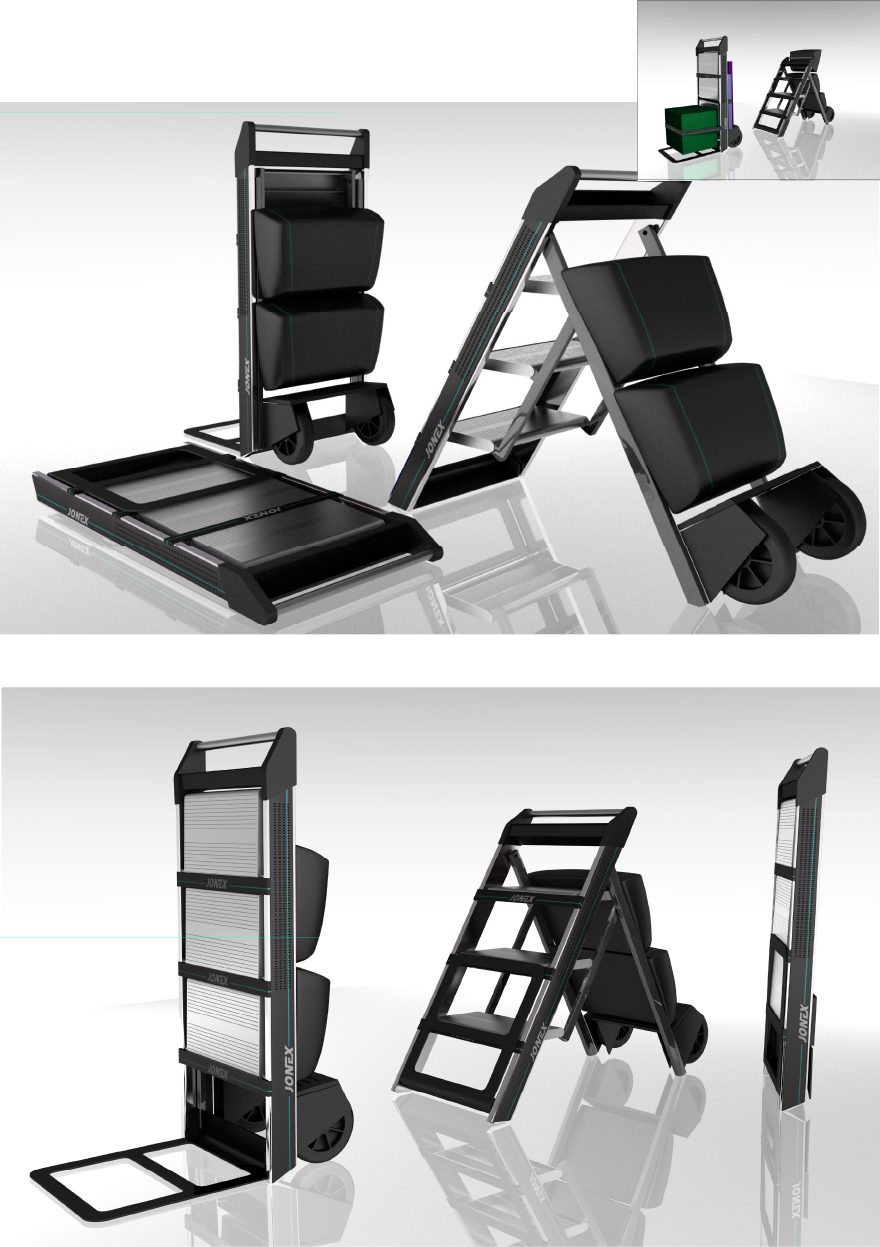
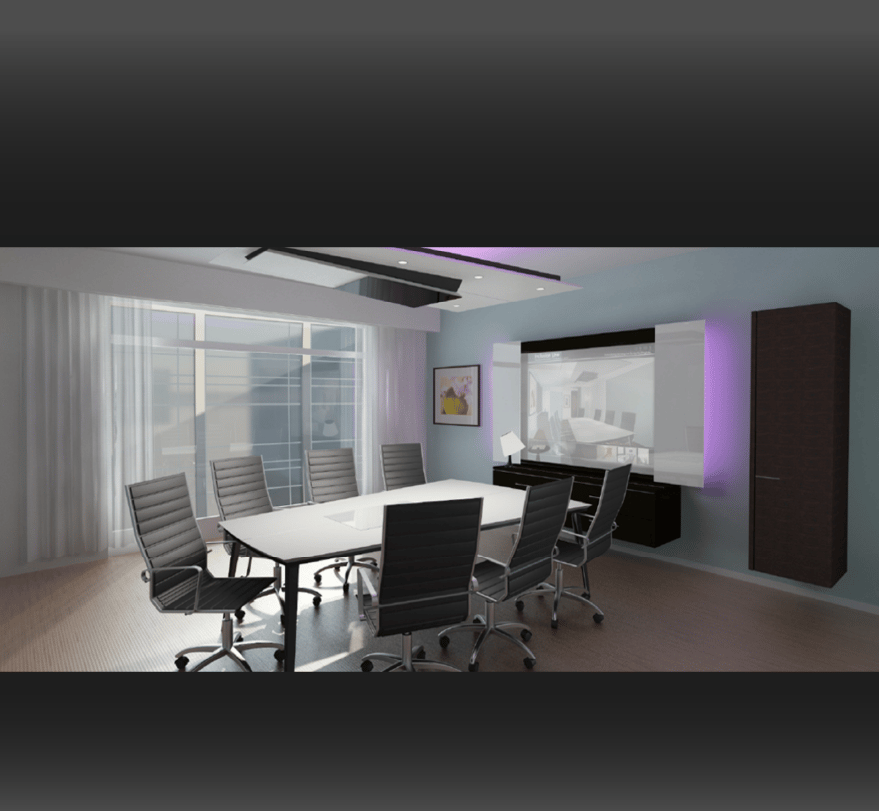
As head of development at STAY/Hovedokka (Furniture manufacturer), as well as lead designer at STAY (Hotel interior design), I learn alot about furniture production and wood/plywood constructions. Several tours to fairs also gave me the insight to how important it is to have good knowledge of the latest in fasteners and new materials.
I also developed a chair of form pressed laminated wood specially designed for obese people. Understanding the process for creating press tooling for lamination was a major learning, as well as working with ergonomics for obesity.
Skill sets: Wood production and constructions (Flatpack and laminated wood), Furniture design, Interior design
WOOD/FURNITURE PRODUCTION
FLATPACK AND LAMINATED WOOD
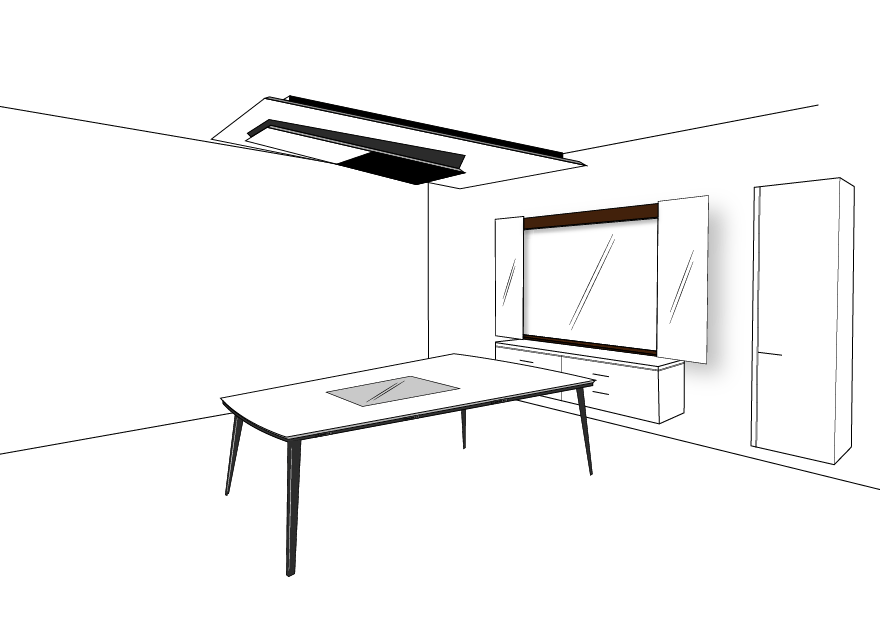
"Communication is not about saying what we think. Communication is about ensuring others hear what we mean." Simon Sinek
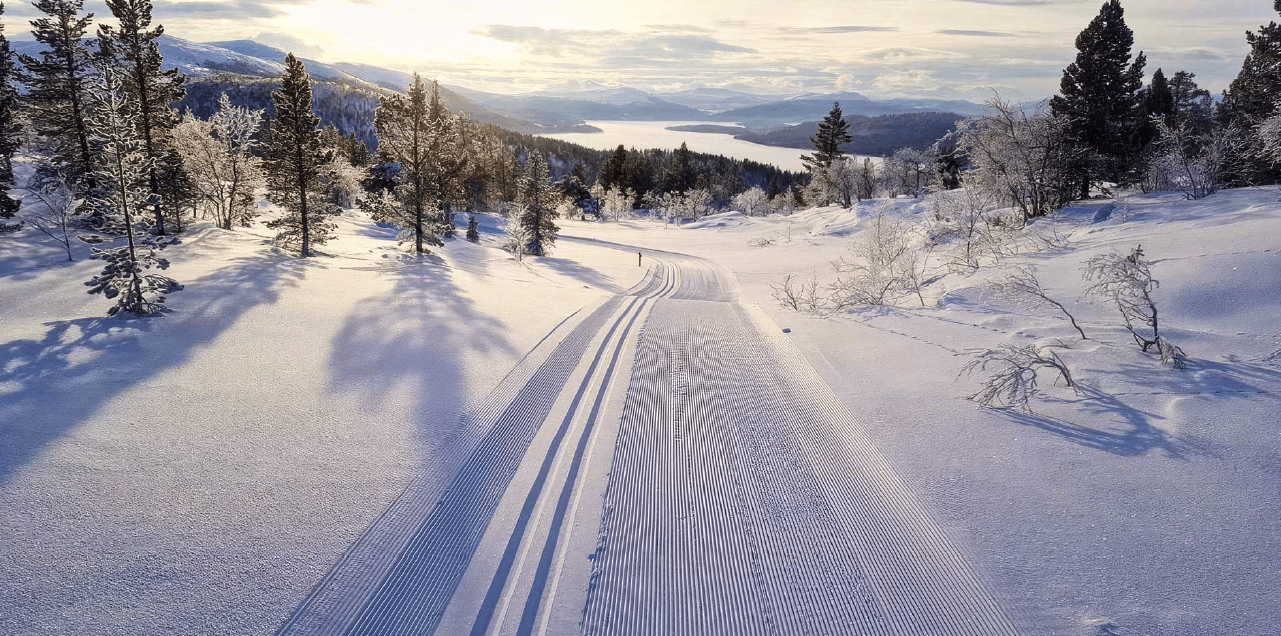
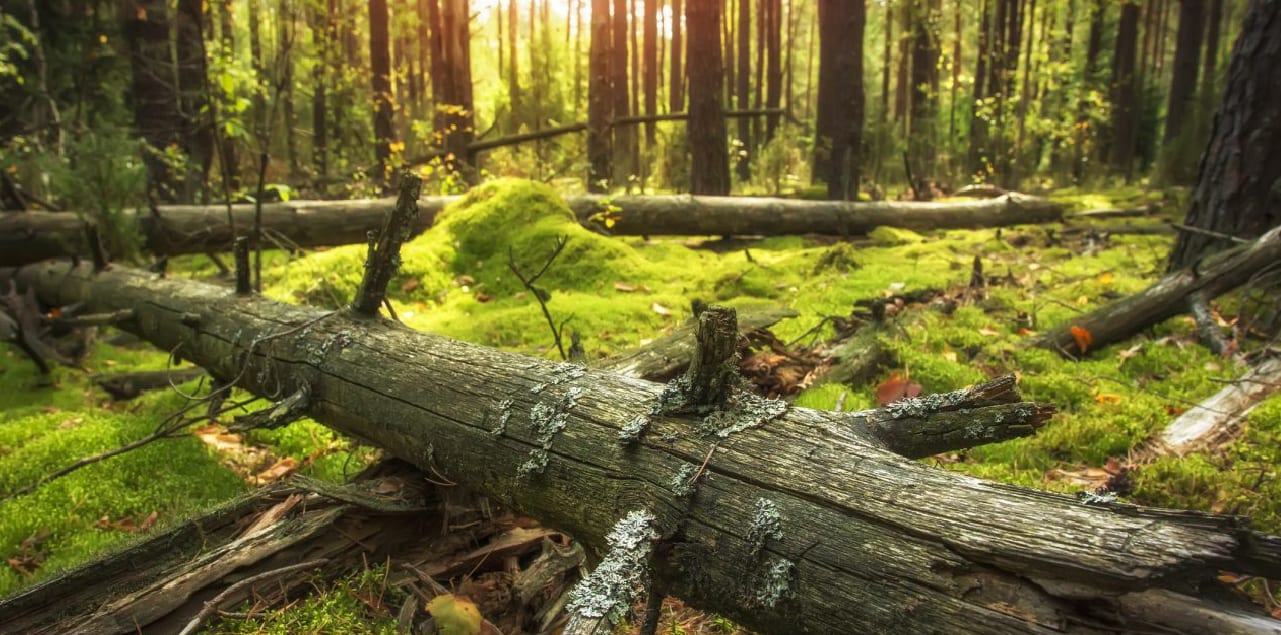
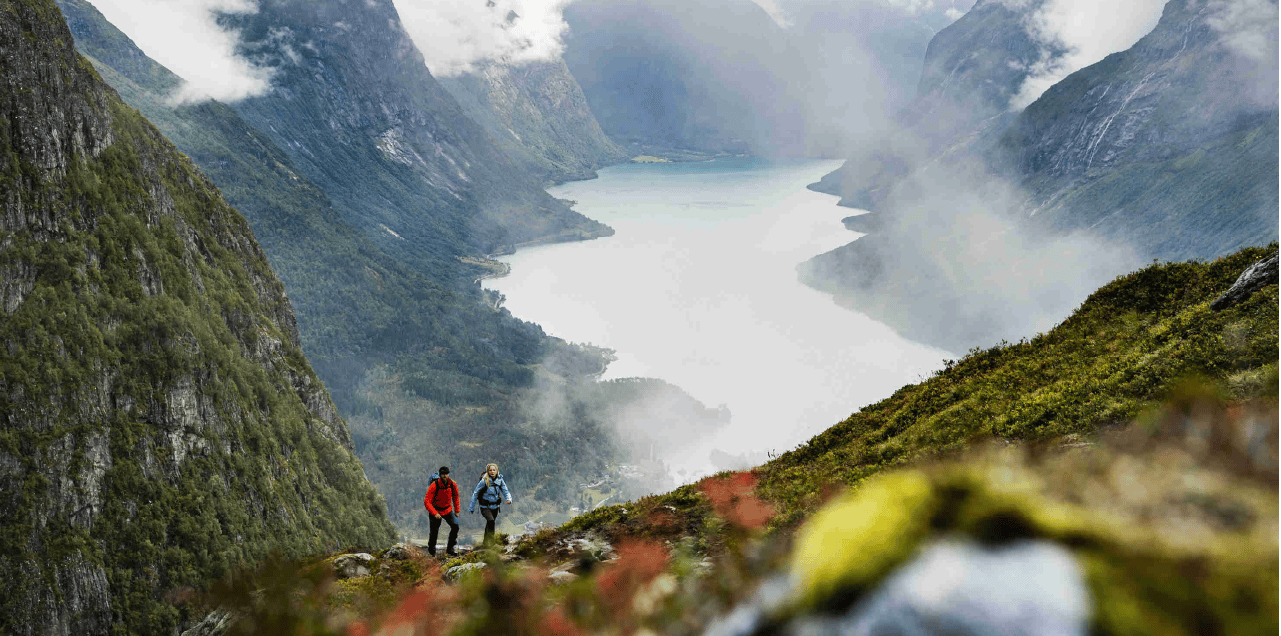
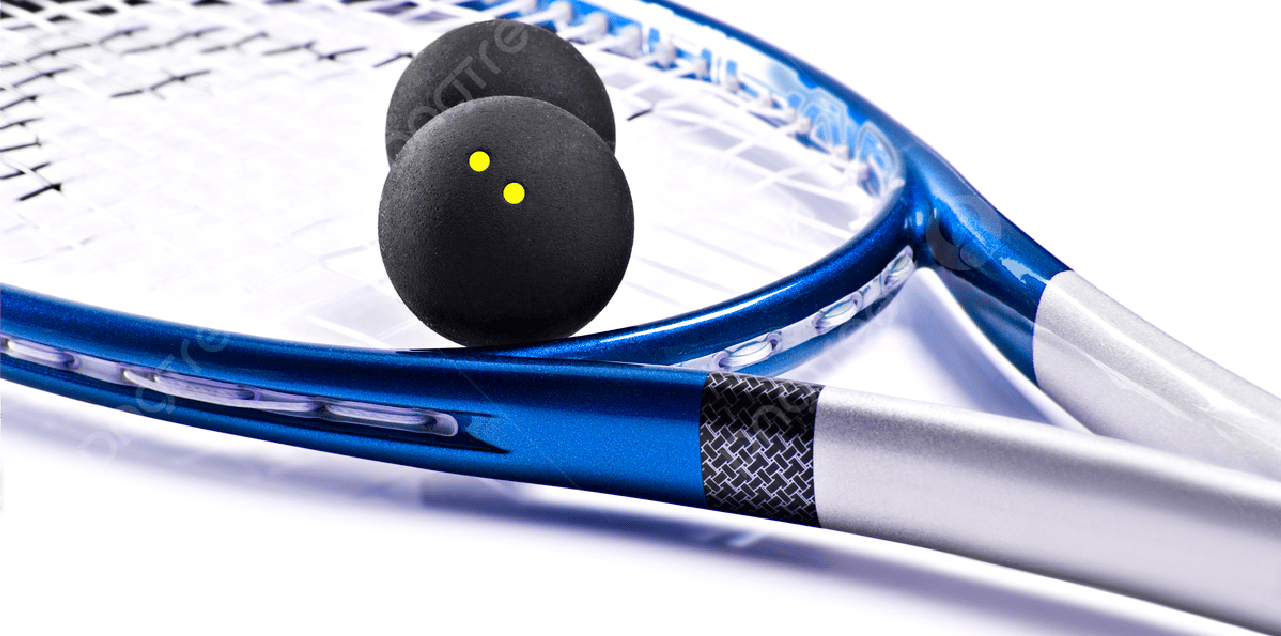
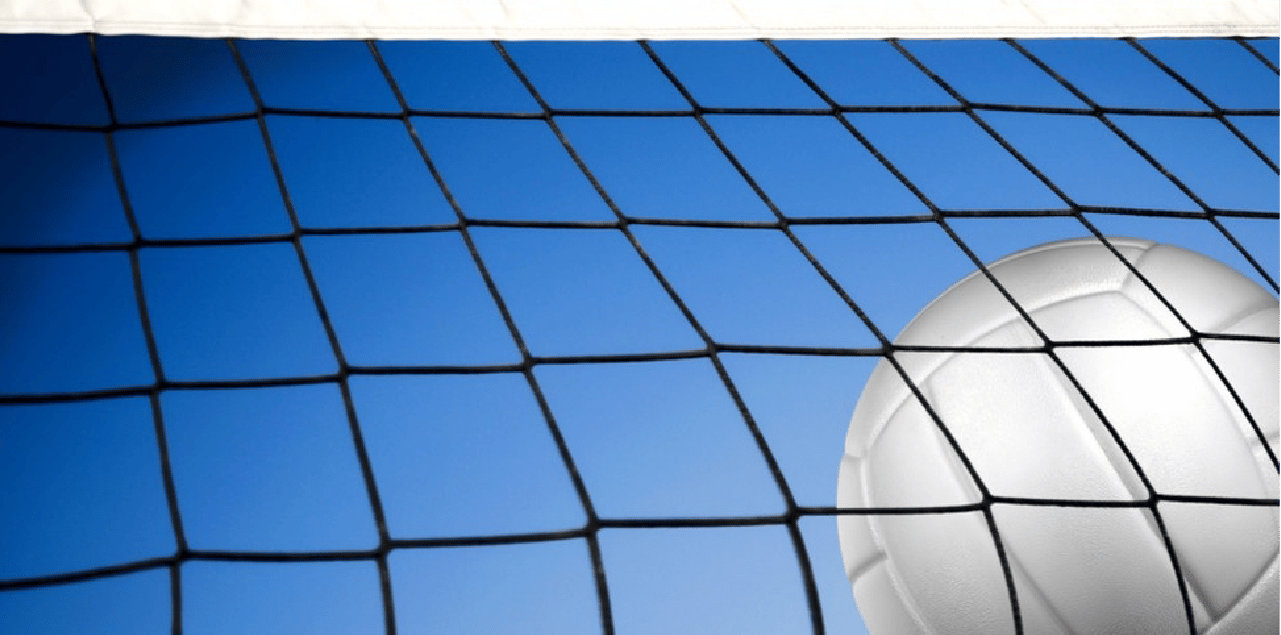
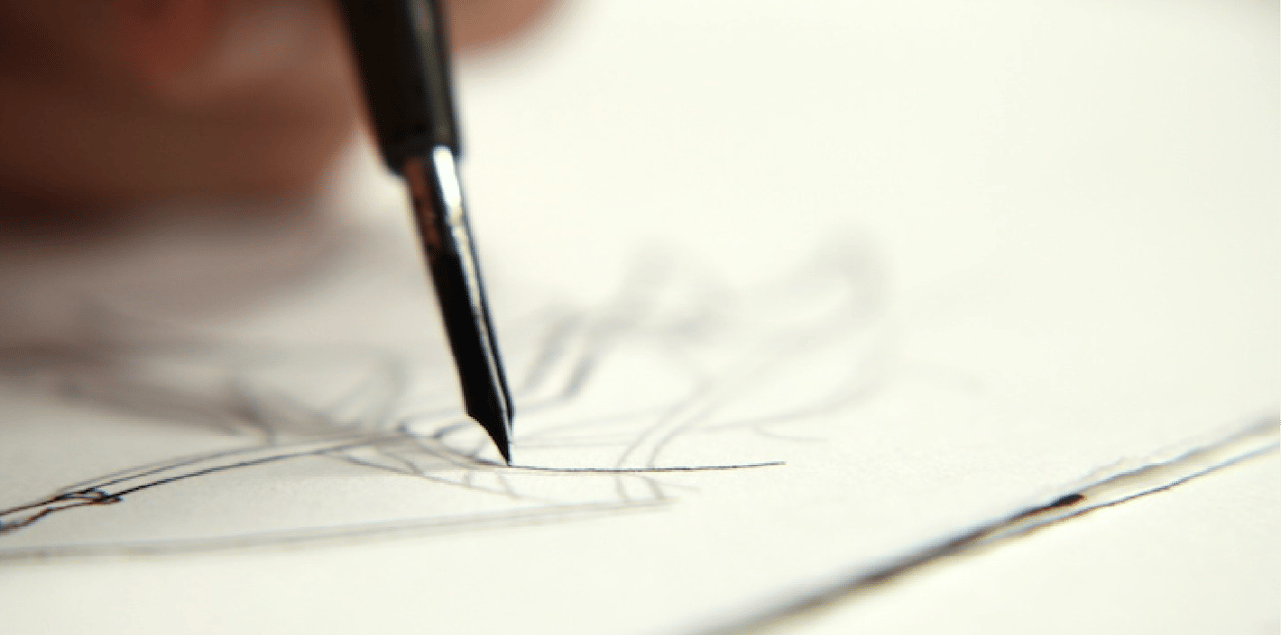
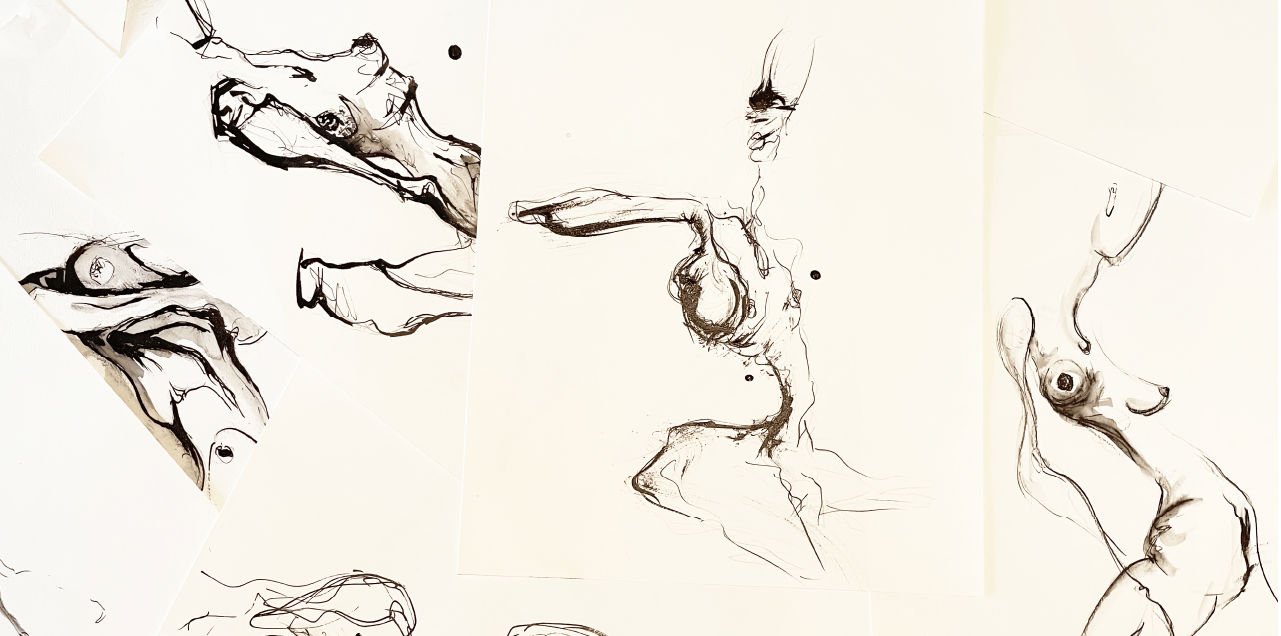
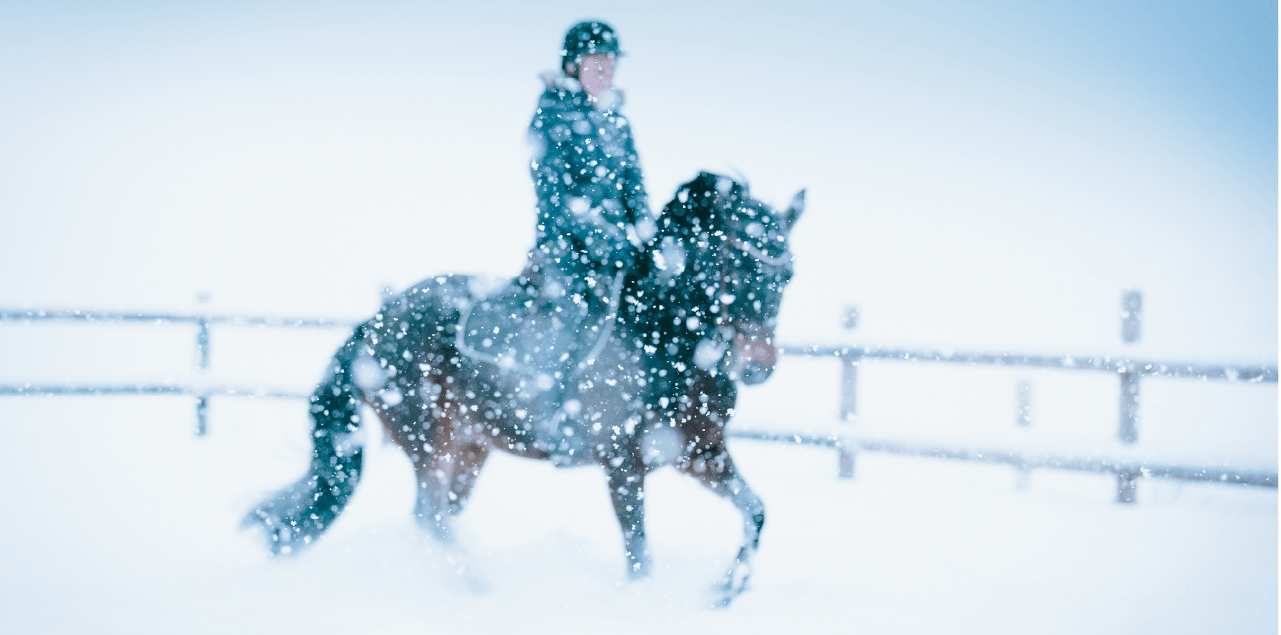
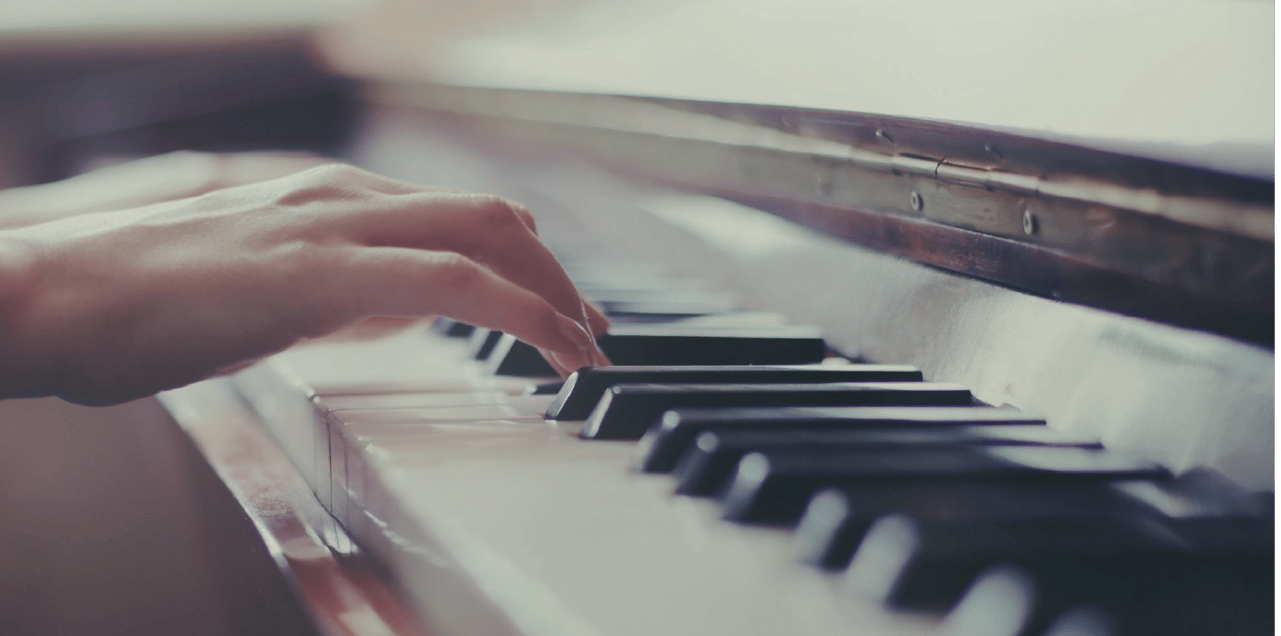
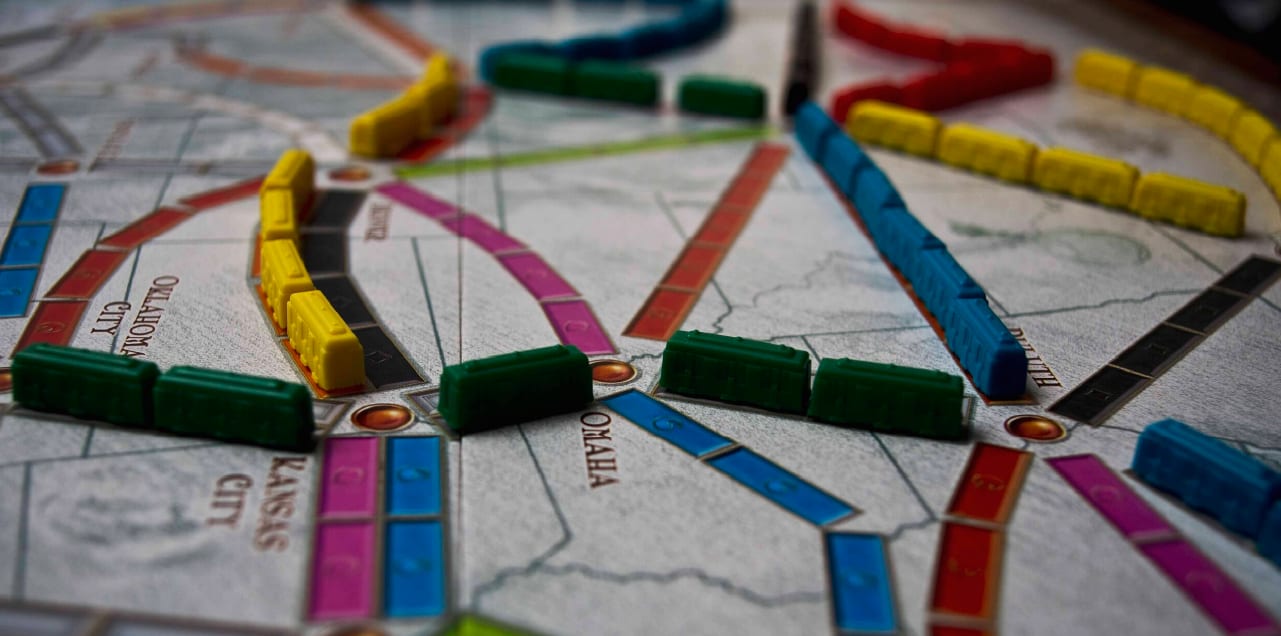
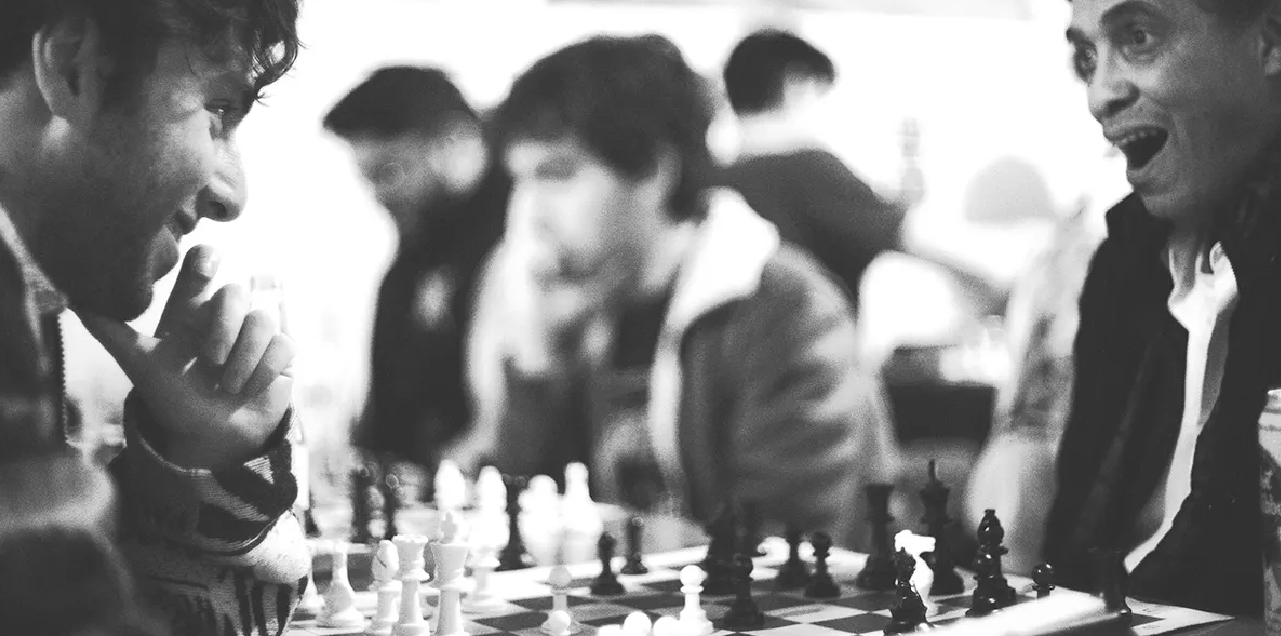